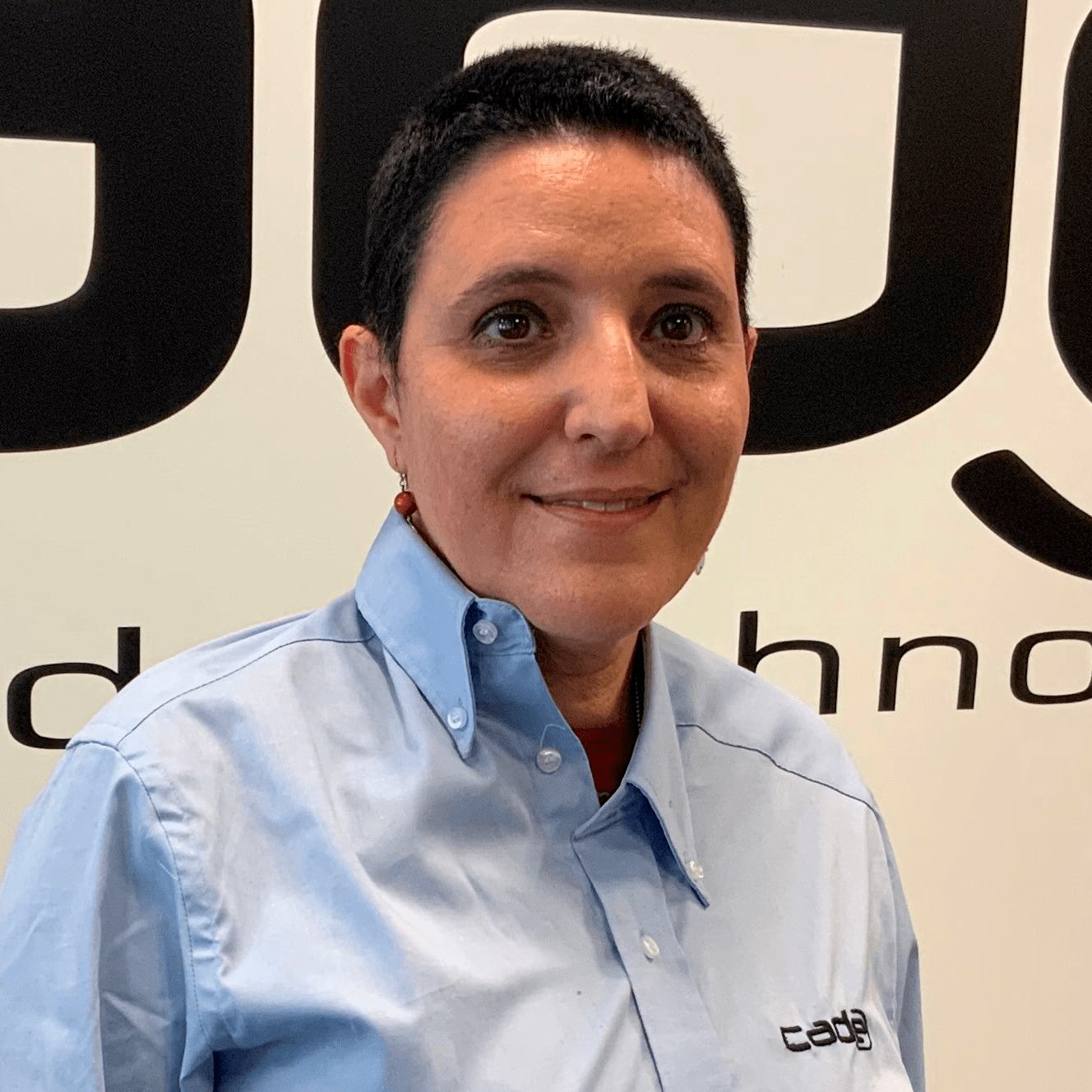
Written by Mili Bueno Rivas
Energy efficiency is key in the oil refining sector, and has a direct impact on the reduction of CO2 emissions generated by its activity.
I have always had a number in my head. From all the OPEX that a refinery has, almost 60% are energy costs… and that’s right. In the vast majority of studies, I have read, the magic number appears.
A refinery takes a lot of energy to transform crude oil into the high-performance products we know; mainly fuels, but also raw materials for the petrochemical industry, which then produces products as diverse as our children’s toys or the fibres used to make wetsuits, car tyres or the trainers you wear when you go running.
In a refinery, energy is mainly consumed in:
- Crude oil Primary distillation: The incoming oil is heated to temperatures of around 380 ºC and atmospheric pressure to separate it into different fractions according to their boiling range.
- Removal of sulphur and nitrogen from these fractions: The use of catalyst and large amounts of energy is necessary to reduce these pollutants in compliance with environmental legislation.
- The production of other compounds necessary for the production of commercial end products: For example, the improvement of the properties of naphtha or gas oil requires the production of products such as ETBE or alkylate. These ancillary units also consume energy.
- Refineries with deep conversion refining schemes (with VDUs, DCUs and FCCUs; “bottom-of-barrel” units) have a generally higher EII, as a large amount of energy is required to convert shorter atom molecules suitable for final product destination.
Energy efficiency improvement opportunities
A wide variety of energy efficiency improvement actions can be undertaken in a refinery, which, for the reader’s better understanding, I have classified into three large blocks:
1. Energy efficiency in processes
This is continuous improvement every day. It involves moderate investment projects, but it all adds up.
They involve, for example, improvements in heat transfer equipment, but also the implementation of energy management systems, preventive maintenance programmes, the establishment of cleaning routines for heat exchange trains, etc.
Other improvements include the optimisation of operating variables or the improvement of the quality of certain circuits, such as the BFW circuit for steam generation in boilers and cogeneration plants, which could result in a significant reduction in fuel consumption. CADE has extensive experience in this type of studies.
There are many, many refinery streams that contain what is called “low waste heat” (between 80ºC and 130ºC), and that can still be used… I know what you are thinking: that low pressure steam cannot be generated.
That is the usual use that refineries have always wanted to make of it… but there are more possible uses. Do you want to know what they are?
Energy efficiency studies are the tools that allow us to identify these improvements.
These types of studies have also been carried out by CADE in its almost 20 years of experience.
Let’s remember that everything adds up, and that not all savings come from large CAPEX projects.
2. Use of low-carbon energy sources
This point encloses the use of electrical energy from renewable sources, as well as studies on the replacement of small gas heaters (lower duty heaters… the Coker heater is not taken into account) with electric heaters, for example.
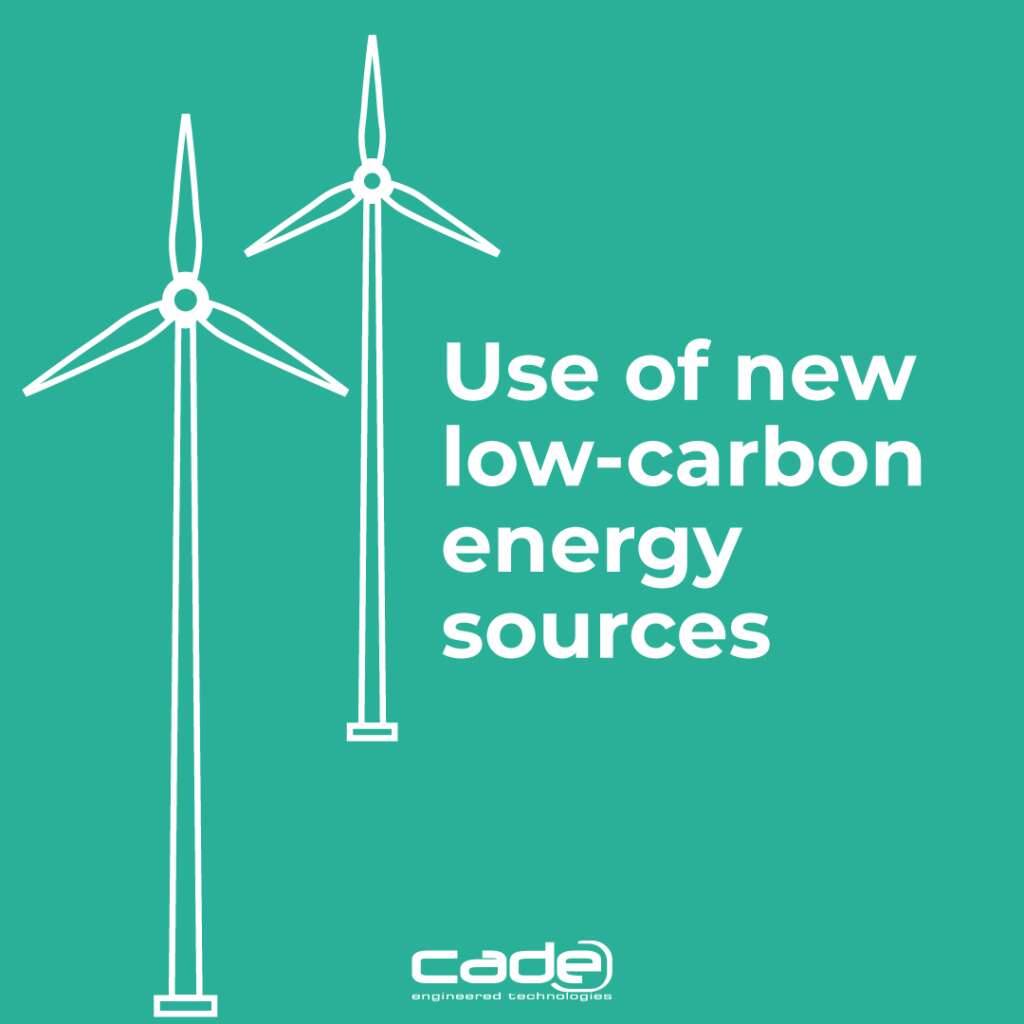
3. Capture of CO2 emitted by the processes
Many refineries are studying and implementing CO2 capture processes, where the CO2 is subsequently used in other sectors such as food or metallurgy.
CADE, which has been working for the Oil & Gas sector for more than 15 years, has extensive experience in the energy consultancy sector. In addition, we have a successful track record with major national and international companies.
Our deep multidisciplinary engineering knowledge and our highly skilled, but, above all, highly committed to excellence in getting the job done right at the first time, together with a solid business management, make CADE an independent leading engineering and consultancy company around technology, equipment and plants within oil&gas and power generation industries.
But they also make CADE a great company to work for every day. Not only big companies are BIG COMPANIES.
Further information
For any query or request for additional information about our services and technologies, please complete the following form: