We Design and Optimize
Equipment, Systems, and Structures
Advanced Numerical Simulation and Computational Analysis for efficiency, sustainability, and innovation.
FEA / FEM Simulation
We apply advanced technologies such as Finite Element Method (FEM) combined with computational modeling and numerical simulation—to design, validate, and verify equipment, systems, and structures.
Our approach ensures industrial asset quality and safety, regulatory compliance, maximized service life, and optimized production costs. These solutions are tailored to enhance efficiency, sustainability, and innovation, positively impacting every stage of a project’s lifecycle.
FEM Simulations Tailored to Each Project
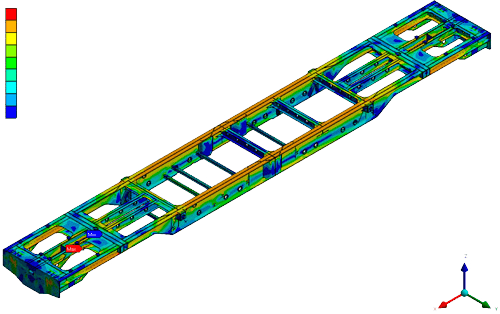
Backed by a team of expert numerical engineers and an in-house High-Performance Computing (HPC) center, we offer cutting-edge FEA and consulting services for:
Design
Validation and verification
Safety and reliability analysis
Digital twin development
Our capabilities span industrial sectors and emerging areas such as hydrogen, biomedical engineering, and additive manufacturing—delivering solutions for optimization and performance improvement from the early R&D phase.
Our deep expertise in ANSYS numerical simulation software and extensive knowledge in code development (Python, APDL scripting, ANSYS ACT customization) positions us as a benchmark in Computer-Aided Engineering (CAE).
We also provide advisory services to companies using ANSYS, helping them develop and implement custom tools and methodologies for process automation, analysis time reduction, and cost optimization.
FEA – Finite Element Analysis
The Finite Element Method (FEM) is a powerful numerical technique for solving complex engineering problems where traditional differential equations are impractical or unsolvable analytically.
In structural engineering, Finite Element Analysis (FEA) is a critical tool for predicting how a design will perform under various loading conditions. It is essential for the design and verification of:
ara el diseño y verificación de:
Projects
Clients
Countries
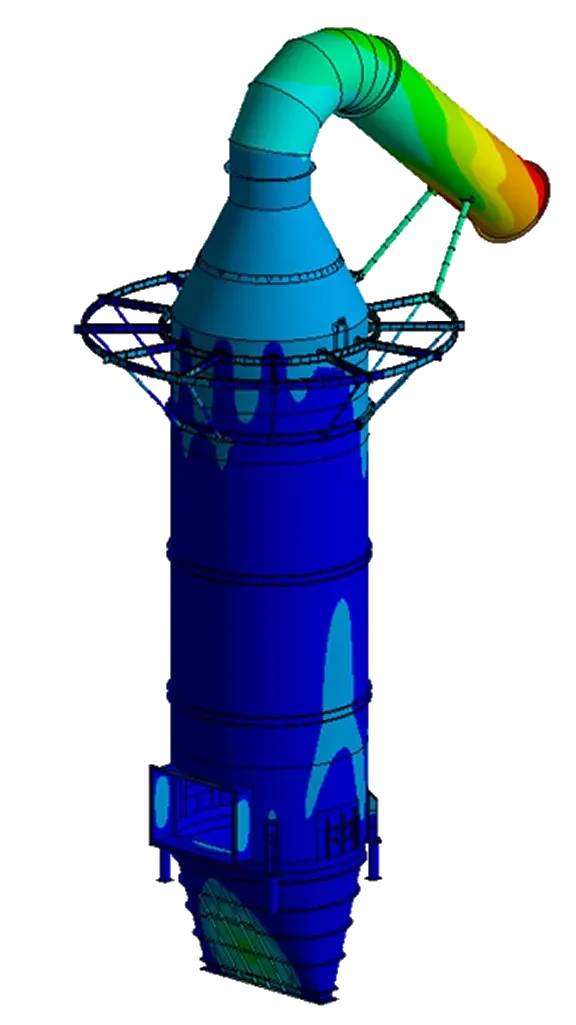
Industrial Sectors Covered:
Metal structures
Pressure equipment
Silos and tanks
Cranes and lifting systems
Heavy machinery
Welded joint design
Vibration analysis
Component optimization
Other Applications:
Topological design optimization
Validation of parts made by additive manufacturing
Prosthesis design
Cardiovascular behavior simulation
Medical device design
Simulation of biological processes and structures
FEM Capabilities Include:
Static structural analysis
Thermal analysis (steady-state and transient)
Dynamic analysis (modal, harmonic, spectral, PSD, explicit, etc.)
Nonlinear analysis (geometric, material, or boundary condition nonlinearity)
Remaining life, fatigue, and creep-fatigue evaluation
Fracture mechanics simulation
CHT (Conjugate Heat Transfer)
Welding process simulation and PWHT analysis
Composite materials, joints, and non-metallic materials analysis
Topology optimization
MBD – Multibody Dynamics
Development of custom tools for automation and process optimization
Some of
Our Solutions
Railway
- Frames ˗ supporting structures
- Cabins and wagons
- Suspension systems ˗ rolling systems
- Determination of aerodynamic coefficients
- Evaluation of vibration phenomena
- Simulation of load states (wind, tunnel entrances and exits, train passage, etc.)
- Analysis of ventilation and air conditioning systems
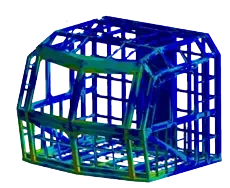
Naval & Defense
- Submarine hull
- Evaluation of elements of the sealed casing (horn shutter, filters, actuators, etc)
- Structural behavior evaluation of hatches
- Design and calculation of piping and duct systems
- Evaluation of pipe components and online elements (valves,
- Pressure equipment (exchangers, vessels, …)
- Dynamic and rotating equipment
- Charging elements
- Evaluation of components with some type of defectology (ovalizations, deformations, loss of thickness, cracks, …)
- Performance of tests
- CFD analysis (internal and external flows)
- Simulation of welding processes
- Root-cause analysis
- Hydraulic and pneumatic system
Oil & Gas
- Asset assessment
- fitness for service analysis
- root cause analysis
- boiler equipment:
- chimneys and torches
- pipelines
- pressure vessels
- heat exchangers
- reactors
- columns
- towers
- tanks
- industrial chimneys
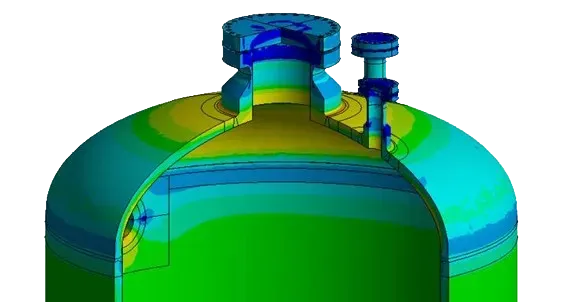
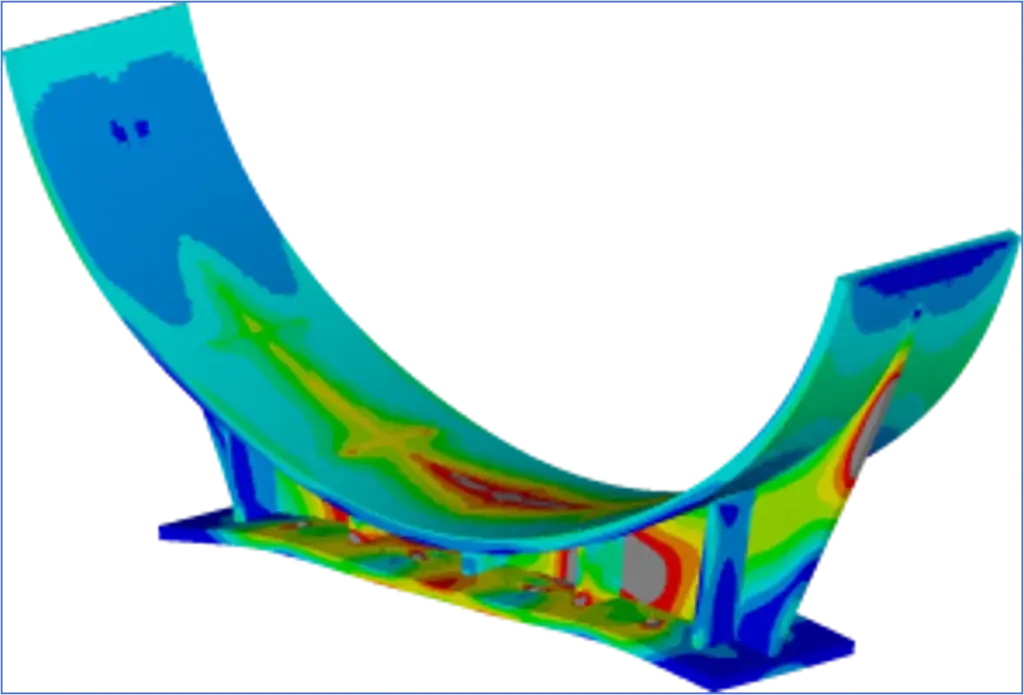
Automotive
- Structural elements
- Engines
- Valves
- Braking systems
- Ventilation systems
- Additive manufacturing
- Topological optimization
- Welding
- Defectology
- Root-cause analysis
- Prototype production
- Impact simulation
- Vibration and noise analysis
- Outdoor aerodynamics
- Refrigeration / climate systems
- Hydraulic systems, pneumatic
- OEM / ODM products
- Industrial vehicles and cargo vehicles (frames, cargo containers, refrigerated containers, etc.)
- Tooling for assembly lines
- Lifting systems
- Paint booths (interior aerodynamics)
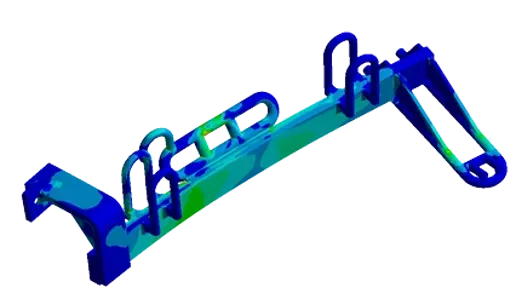
Energy Generation
- Structural integrity
- Fluid dynamic simulation (indoor and outdoor)
- Asset assessment
- Fitness for service analysis
- Root cause analysis
- Chimneys and torches
- Boiler equipment:
- By-pass systems
- Diverters
- Dampers
- Valves (guillotine, butterfly, etc.)
- Gas distributors
- Silencers
- Large diameter ducts
- Pressure equipment
- Exchangers
- Other parts of the equipment
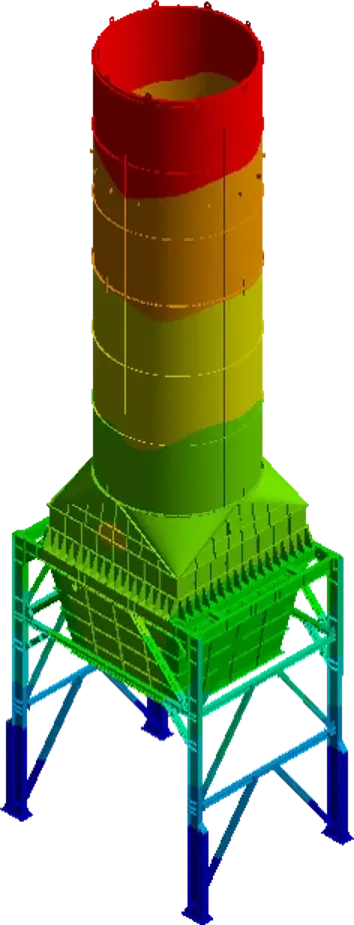
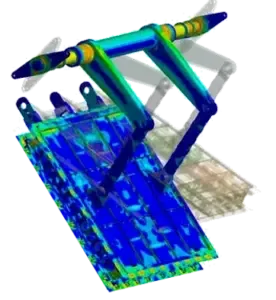
Renewable Energy
- Solar trackers (1 or 2 axis solar trackers)
- Concentration structures (parabolic through collector, heliostato, stirling dish, HCPV, etc.)
- Fixed solar structures
- Piping system
- power plants (static equipment and exchangers)
- Dynamic and rotating equipment
- Hydraulic systems (valve)
- Electrification systems
- Wind generators (foundation, towers, bushings, transmission systems, etc.)
- Behavior of screwed joints
- Assessment of useful life or remaining life
- Preventive and corrective maintenance plan
- Root cause analysis
- Definition of the plan of corrective measures
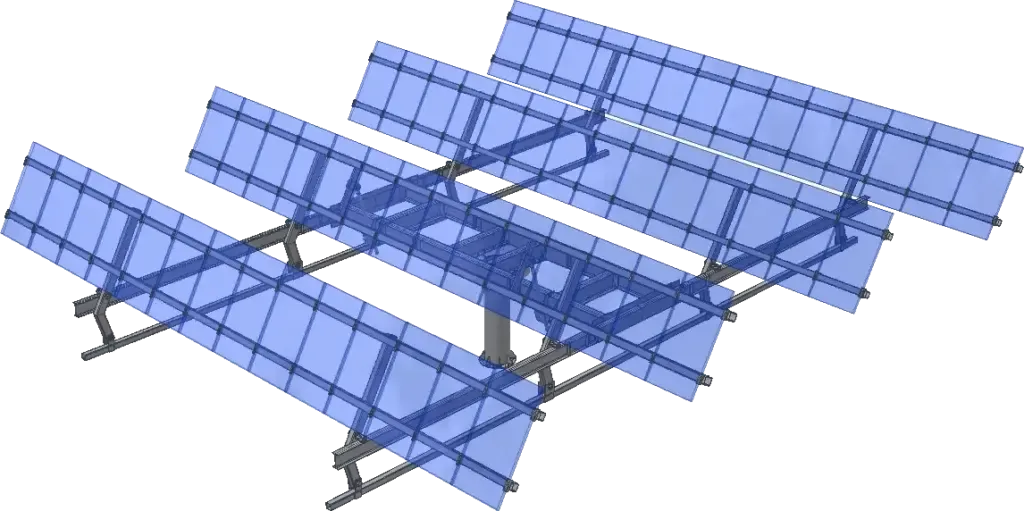
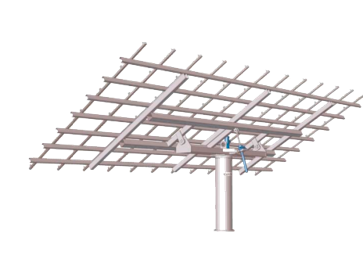
Big structures, special and modular structures
- Steel structures
- Industrial roofs
- Cranes / bridges cranes
- Port cranes
- Channeling infrastructures
- Communication and electrification towers
- Flat or space structural systems composed of bars, plates, walls, sheets, solids and contact elements
- Singular buildings (hangares, etc.)
- Design of modular structures (industrial warehouses, agricultural and livestock warehouses, greenhouses, awnings and canopies, etc.)
- Structures of labeling and corporate image
- Simulation of screwed joints
- Welding process simulation
Lifting equipment, transportation, and cargo handling
- Load lifting systems
- Cranes / bridges crane
- Lifting platforms and benches
- Sts, rtg cranes (port cranes)
- Forklifts
- Conveyor belts
- Work platforms
Piping Systems
- Stress and flexibility analysis
- Support design
- Special pipes (large diameters, large thicknesses, non-conventional geometries, etc.)
- Online element analysis (TEES, connections, valves, etc.)
- Definition and analysis of expansion joints and compensators (metallic, textiles)
- Analysis of elements under critical loads (high pressures and high temperatures)
- Analysis of thermal trace systems
- Analysis of elements under external pressure or vacuum
- Root cause analysis and fault detection
- Inspection (thickness measurement, 3d scan, corrosion, etc.)
- Definition of measure plan
- Preventive and corrective maintenance
Ducts
- Design and simulation of:
- By-pass systems
- Diverters
- Dampers
- Valves
- Gas distributors
- Silencers
- Large diameter conduits
- Design of support systems
- Online element analysis (tees, connections,
- Valves…etc)
- Definition and analysis of expansion joints and
- Compensators (metallic, textiles)
- Analysis of elements under critical load(high pressures and high temperatures)
- Analysis of elements subject to external pressure or vacuum.
- Fluid dynamic simulation
- Root cause analysis and fault detection
- Inspection (thickness measurement, 3d scan,
- Corrosion, etc.)
- Definition of measure plan
- Preventive and corrective maintenance
Urban & Industrial Furniture
- Lighting and lighting system (scales, columns and luminaires)
- Sewer systems, covers, grids …
- Canopies and pergolas
- Urban furniture
- Recreational furniture (children’s parks and sports furniture)
- Industrial storage systems
- Palletization shelves
- Industrial stairs
- Metallic and wood cabinets
- Modular and configurable furniture
- Stands
- Tents
- Structures of labeling and corporate image
- CE marking
Architecture & civil works
- Buildings / singular buildings
- Covers
- Lifts and staircase
- Electrical equipment containers
- Channeling infrastructures
- Purification of plants
- Adaptation of existing warehouses
- Ventilation and air conditioning systems
- Fire doors
- Explosion doors and windows
- Dynamic analysis and vibrations by resonances
- Seismic analysis
Design & Calculation of joints
WELDED JOINTS
- Simulation of welding processes
- Strength calculation of welds
- Construction details design
BOLTED JOINTS
- Design and calculation of conventional screwed joints
- Design and calculation of special screwed joints
- Friction joints
- Definition of tightening torques
- Definition of procedure and tightening sequences
- Conventional screws and high strength screws
- Fatigue calculation
- Palletization shelves
FLANGED JOINTS
- Design and calculation of the joint flanges
- Screw dimensioning
- Definition of tightening torques
- Definition of procedure and tightening sequences
- Assessment of the sealing of the joint
- Base plates and anchoring systems to concrete
Non-metallic Materials
- Pressure vessels cpr
- Design of plastic parts and components
- Design of reinforced polymeric or plastic parts and components
- Plastic injection process simulation
- Material search
- Materials check
- Design of reactors and equipment for plastics production