A la hora de diseñar un equipo a presión, la elección del código de diseño es una de las principales decisiones que debe ser tomada; deben ser tenidos en cuenta requisitos de la norma no sólo relativos a las condiciones de diseño, sino también de fabricación e inspección. Uno de los factores con más peso en esta toma de decisión es el posible ahorro de material en aquellos equipos que sean más críticos y que requieran el uso de materiales de alta resistencia o en equipos de grandes dimensiones, en los que la obtención de un espesor más optimizado tiene un gran impacto no sólo a nivel económico, sino también en la fabricación de dicho equipo.
Una de las principales normas de referencia para equipos a presión es ASME VIII, tanto la división 1 como la división 2. Desde un punto de vista de diseño e inspección, si comparamos ambas metodologías:
- ASME VIII Div 1: obtenemos diseños con mayores espesores al considerar un factor de seguridad SF=3.5; no obstante, la exigencia de ensayos e inspecciones es más laxa.
- ASME VIII Div 2: la norma permite una optimización de espesores con respecto a los obtenidos en la división 1 al considerar en su formulación un factor de seguridad SF=2.4, sin embargo, se requiere un mayor número de ensayos e inspecciones.
Otros requisitos propios de la división 2 son la emisión de la UDS (User Design Specification) por parte del propietario del equipo, así como de la MDR (Manufacturer Design Report) por el fabricante de dicho equipo; en ambos casos se requiere la certificación de los documentos por parte de un Professional Engineer.
Desde la edición de 2017, en la División 2 se ha incluido la posibilidad de diseñar un equipo denominado como Clase 1 que por lo general considera una mayor tensión admisible del material, con un factor de seguridad SF=3. Esta nueva clase permite llevar a cabo diseños por fórmula con espesores más optimizados.
Tensión admisible | ||
División 1 | División 2 | |
Tabla 1A/B ASME II Part D | Clase 1 | Clase 2 |
Tabla 2A/B ASME II Part D | Tabla 5A/B ASME II Part D |
Por tanto, a la hora de calcular equipos según ASME VIII Div 2 es necesario especificar la clase de equipo considerada (Clase 1 / Clase 2). No obstante, existen otras diferencias entre ambos métodos que van más allá del factor de seguridad considerado en la formulación y que deben ser tenidos en cuenta:
- En el caso de equipos con servicio no cíclico (menos de 1000 ciclos P-T), no es necesario la certificación de la UDS por un Professional Engineer; no obstante, la revisión de la UDS sigue siendo necesaria; únicamente es requerida la certificación de la UDS cuando sea necesario un análisis a fatiga.
- Para equipos Clase 1, la MDR tiene que ser certificada por un Professional Engineer únicamente cuando i) algún componente del equipo es diseñado con la Parte 5 de la norma ASME VIII Div 2 debido a que su diseño no está cubierto por la formulación de la Parte 4 de la norma ASME VIII Div 2, ii) si es necesario llevar a cabo un análisis a fatiga o iii) si se ha realizado un análisis dinámico en el caso de sismo.
- Los equipos Clase 1 deberán ser diseñados con la Parte 4 de la norma ASME VIII Div 2; no obstante, cuando no exista una regla en la Parte 4 para cubrir un diseño específico, podrá realizarse el diseño usando la Parte 5 de la norma, considerando todas las cargas incluidas en la UDS. En ningún caso se podrá emplear la Parte 5 para sustituir requisitos de la Parte 4.
Habitualmente, la norma elegida para el diseño de equipos de mayores espesores y dimensiones ha sido ASME BPVC VIII Div 2 por el ahorro de material, ya que la metodología de diseño en la que está basada esta norma es más precisa con respecto a la seguida en ASME BPVC VIII Div 1. La división 2 está basada en un criterio de tensiones de Von Mises mientras que la División 1 se fundamenta en la teoría de la máxima tensión principal, es decir, la rotura se produce cuando la mayor de las tensiones principales alcanza un valor límite. Por lo tanto, la introducción de equipos Clase 1 en la División 2 da mayor flexibilidad a la hora de decidir qué norma de diseño es la más eficiente desde un punto de vista económico.
No obstante, cuando se busca un diseño más optimizado y competitivo, la mejor opción es el diseño del equipo mediante la Parte 5 de ASME VIII Div 2: Diseño por análisis. Esta parte de la norma se basa en los resultados obtenidos mediante simulación numérica evaluando la protección de los diferentes componentes del equipo frente a modos de fallo tales como colapso plástico, pandeo, fallo local, fatiga. La norma contempla la realización de cálculos complejos en los que se contempla tanto la no linealidad del material (comportamiento plástico) como las no linealidades geométricas.
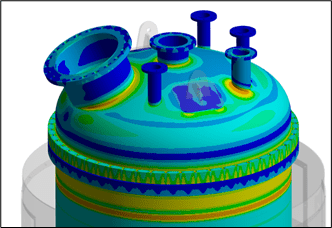
En CADE tenemos una amplia experiencia en el diseño de equipos a presión tanto por fórmula, calculando tanto con ASME BPVC VIII División 1 como con División 2, así como en el diseño por análisis que implica la ejecución de cálculos más complejos a partir de modelos de elementos finitos y la correspondiente evaluación de los diferentes modos de fallo requeridos por la norma. Gracias a nuestro potente equipo de trabajo multidisciplinar, en CADE ofrecemos un acompañamiento integral abarcando el ciclo de vida completo de un equipo, ya que participamos tanto en las fases preliminares de prediseño y diseño como en etapas más avanzadas de operación y parada de equipos en planta, en las que también se evalúa la integridad mecánica de los equipos debido a posibles defectos o fallos estructurales mediante análisis Fitness for Service. En este tipo de estudios, es crítico poseer un expertise como el de CADE en mecanismos de daño para poder realizar una evaluación adecuada de aptitud al servicio y determinar si el equipo evaluado ha de ser reemplazado o, por el contrario, puede continuar en servicio, para lo cual será necesario determinar de forma correcta la vida remanente.