In the Oil & Gas industry, and in the particular case of hydrocarbon reactors, equipment subjected to high operating pressures and temperatures, the selection of the material is mainly oriented to the use of 2 1/4 Cr-1Mo steels due to the high performance of the material at a mechanical level, since, compared to other steel grades, Not only does it allow for more weight-optimized designs, but it also features greater resistance to hydrogen attack, reduced susceptibility to embrittlement, and increased resistance to delamination of the weld coating.
The presence of hydrogen is inherent in hydrocarbon reactors, which means that this type of equipment is one of the most critical within refineries and industrial plants; Special precautions need to be taken during low-temperature load scenarios, such as in the hydrostatic test or during start-up or shutdown, due to the increased risk of brittle fracture failure. To this end, it is recommended to develop MPT Minimum Pressurization Temperature curves that ensure safe pressurization of the reactor without risk of embrittlement.
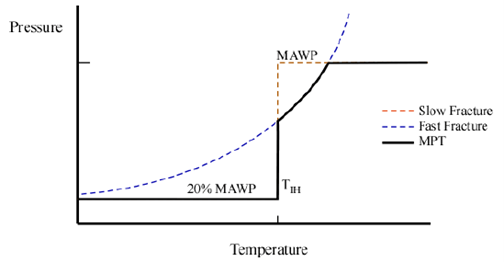
In addition, if we take into account that the presence of pores or inclusions is unavoidable in the manufacturing processes of a reactor, and that these defects can facilitate the propagation of cracks, it is becoming increasingly common to predict the defective failure of a reactor from the design stage, in which the characterization of the defect is based on the minimum detectable crack size through inspection techniques non-destructive. When determining the minimum crack size, it is not recommended to overlook the different factors that influence the quality of the inspections carried out, such as the geometry of the reactor, accessibility, as well as limitations associated with the reading equipment itself and the skill of the operator in charge of the measurements.
In fracture mechanics calculations, another critical parameter along with crack morphology is the position of the fracture. Since a crack is prone to propagation when in a tensile stress field, the main factors to consider when defining the position of the potential defect are both the triaxiality that promotes crack growth, and the presence of residual stresses associated with welding processes. The presence of residual stresses resulting from non-uniform temperature distributions during welding processes, especially during the cooling stage, can trigger crack initiation, growth, and potential propagation.
Thanks to the advanced simulation resources that we have at CADE, it is possible to identify with great precision the most susceptible regions in which a defect not detected by the usual inspection techniques can grow and spread, which implies that the fragile invoice failure scenario becomes a potential failure phenomenon and that, therefore, it must be evaluated. The characterization of crack-like plane defects is covered by Part 9 of API code 579/ASME FFS-1.
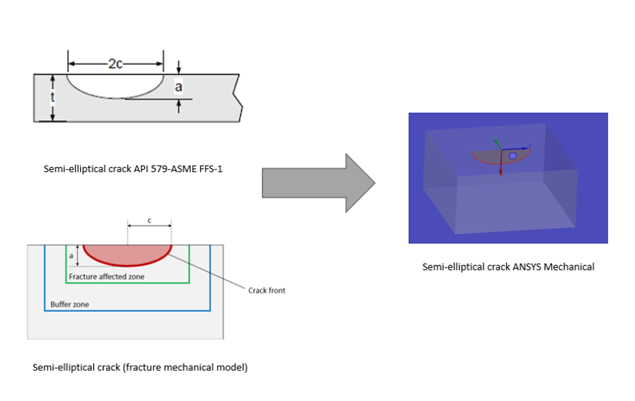
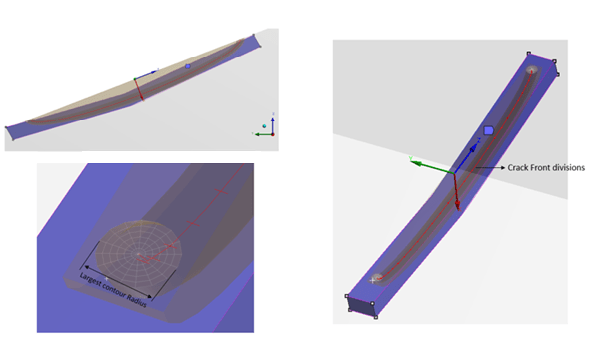
The main challenges in this type of calculation lie both in the definition of the thermodependent properties of the materials at high temperatures, as well as the complexity associated with the numerical calculation itself, in which it is necessary to implement the low rigidity of the molten material and the deformations of the different components during heating and cooling between passes.
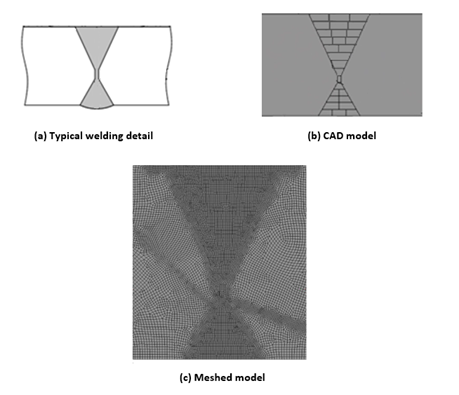
CADE‘s expertise and know-how in both the field of advanced simulation and materials technology positions us as a national and international benchmark in the execution of this type of calculation. Once the stress distributions have been obtained, the regions most susceptible to crack propagation are identified.
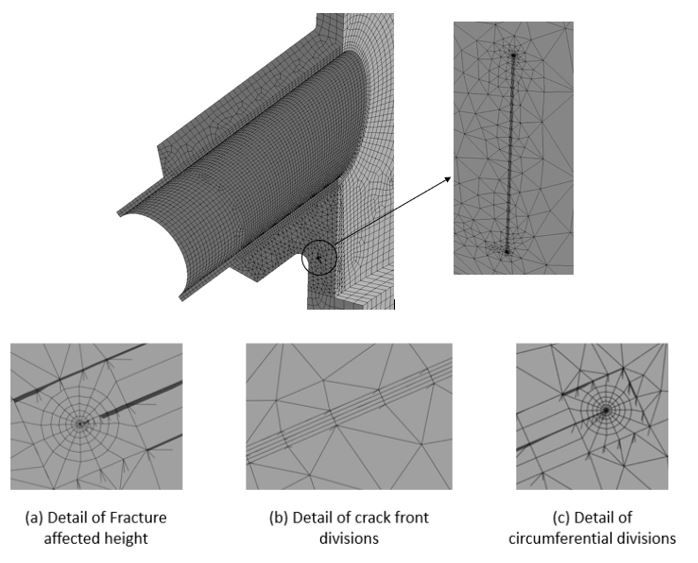
The structural integrity of a brittle fracture-susceptible reactor in which the crack has been explicitly implemented is accomplished by performing a Level 3 Fitness for Service Analysis to API 579/ASME FFS-1 Part 9 and using the FAD fracture mechanics diagrams
In the event that the assumed defect is considered unstable according to the requirements of the code, it would be necessary to carry out a redesign of the reactor, either at a geometric level or in terms of operating conditions. Other alternatives that do not involve going through a redesign phase are aimed at the implementation of optimized inspection programs and/or the development of a digital twin of the reactor that allows continuous monitoring in anticipation of the potential growth of the crack and, therefore, the possible failure of the equipment.
Further information:
For any question or further information request about our services and technologies, please complete the following form: