Current problems for owners and operators of renewable energy plants based on a steam cycle are usually related to the use of equipment that has been in operation for a long time. Most of the time, such equipment is conditioned by previous repairs, loss of efficiency, and deviations between the initial design and real operating conditions.
Besides these common issues, specifically, CSP plants (Concentrated Solar Power plants) are mechanically conditioned by the actual operation of its power cycles, which involves daily startup/shutdown cycling operations and fosters main equipment fouling and corrosion. For these reasons, a new approach is necessary to attack the operation and maintenance activities of concentrated solar plants.
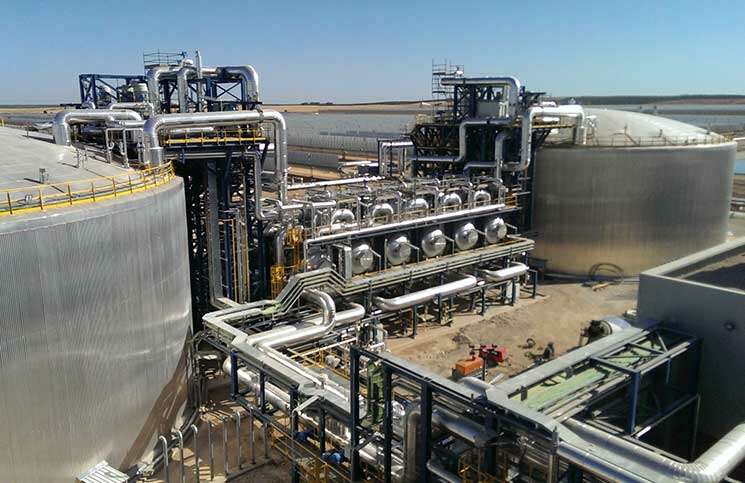
‘InCycle’ analysis methodology allows to systematically and specifically address the condition of steam cycle plants and its key factors, to improve their efficiency, increase their service life, and reduce regular failures and shutdowns for maintenance.
OPERATION CONDITIONS
- Data registered at DCS
- Local data collection
NON DESTRUCTIVE ESSAYS
- Sample Analysis
- Borescopies
- Thickness Measurement
- Corrosion Coupons
- Thermal Characterization
- Hydraulic Characterization
- Thermal Equivalent Model
- Hydraulic Equivalent Model
- Fouling mechanisms
Corrosion - Mechanisms
Simulation and Optimization of the Steam Cycle
- Increase performance
Mechanical simulation
- Integrity and Reliability
- Operational limits
- Accumulated Damage
Predictive Models
- Integrity and Reliability
- Operational limits
OPTIMAL OPERATING CONDITIONS OF THE CYCLE
PREDICTIVE MAINTENANCE PLAN
PLANT IMPROVEMENTS
- Sampling system
- Dosing system
- Water quality
Key points of Incycle’s analysis methodology for renewable steam cycles
- Key points identification on-site for data gathering critical node.
- Data evaluation in critical nodes to check its veracity and reliability.
- Plant data collection in critical nodes.
- Equipment characterization: based on actual plant data.
- Generation of equivalent models (thermal, hydraulic and mechanical).
- Integrated optimization of the cycle: performance improvement, reduction of mechanical damage and maintenance interventions. Increase in efficiency and service life.
- Optimization of the monitoring system and the sampling of the water-steam system. Decision-making methodology based on reliable data
- Equipment inspection and sample gathering. Dynamic models of corrosion and fouling.
- Prediction of performance and needs of preventive maintenance.
- Plant upgrades
Value proposition to Plant owners and O&M companies
- Improvement of cycle performance, with a consequent efficiency increase
- Reduction of LCOE
- Increase in equipment service life.
- Reduction of maintenance shutdowns. Predictive Maintenance.
- Improvement of the current monitoring system: Decision making based on true data
Further information:
For any question or further information request aboud our services and technologies, please complete the following form: