Medical Production Line Automation
Collaborative Robotics and Traceability Integration to Optimize Medical Manufacturing
Project
Description
CADE successfully delivered a turnkey EPC project for ULB Medical, aimed at creating an automated production line for the manufacturing of surgical kits. The project included the design, supply, and installation of advanced equipment, along with a management and traceability IT system fully integrated with ULB’s Business Central ERP, enabling real-time operational control.
The production facility is divided into three main areas: a preparation room for materials, a clean room for kit assembly in a contaminant-free environment, and a grey room for final packaging and palletizing. The clean room is equipped with sealing systems and environmental control to ensure full compliance with health and safety regulations.
In addition, collaborative robotic solutions were implemented for palletizing, allowing safe interaction between robots and human operators. The line was designed for future scalability, enabling the addition of a second assembly line without major structural modifications. A robust electrical and IT network was also developed to support production systems, along with a maintenance and training contract for ULB’s personnel.
Strategic
Advantages
Improved Operational Efficiency
Automation of key processes reduces production time and minimizes human error, resulting in a significant productivity increase.
Complete Traceability and Control
ERP system integration enables detailed tracking of each process step, ensuring transparency and regulatory compliance.
Compliance with Health Standards
The clean room and sealing systems ensure a sterile and controlled environment, essential for high-quality medical products.
Long-Term Cost Reduction
Reduced labor dependency, lower material waste, and efficient maintenance translate into significant operational savings.
Daily output of over kits
Clean room workstations under strict environmental control
Automated quality control with machine vision
Next-generation collaborative robots
Project
Scope
Critical Infrastructure
Design and installation of a clean room compliant with health regulations, equipped with advanced environmental control systems, automated conveyor belts, and weighing and sealing equipment to ensure consistent product quality.
Electrical and IT Systems
Deployment of a robust electrical and communication network, including electrical panels and UPS systems, ensuring reliable and secure automation connectivity.
Automation and Collaborative Robotics
Integration of Universal Robots for automatic palletizing, designed to work safely alongside operators and enhance production line efficiency.
Operational Management and Traceability
Development of customized software for real-time tracking, fully integrated with ULB’s Business Central ERP, and prepared for future expansion or adaptation.
The Project in
Images
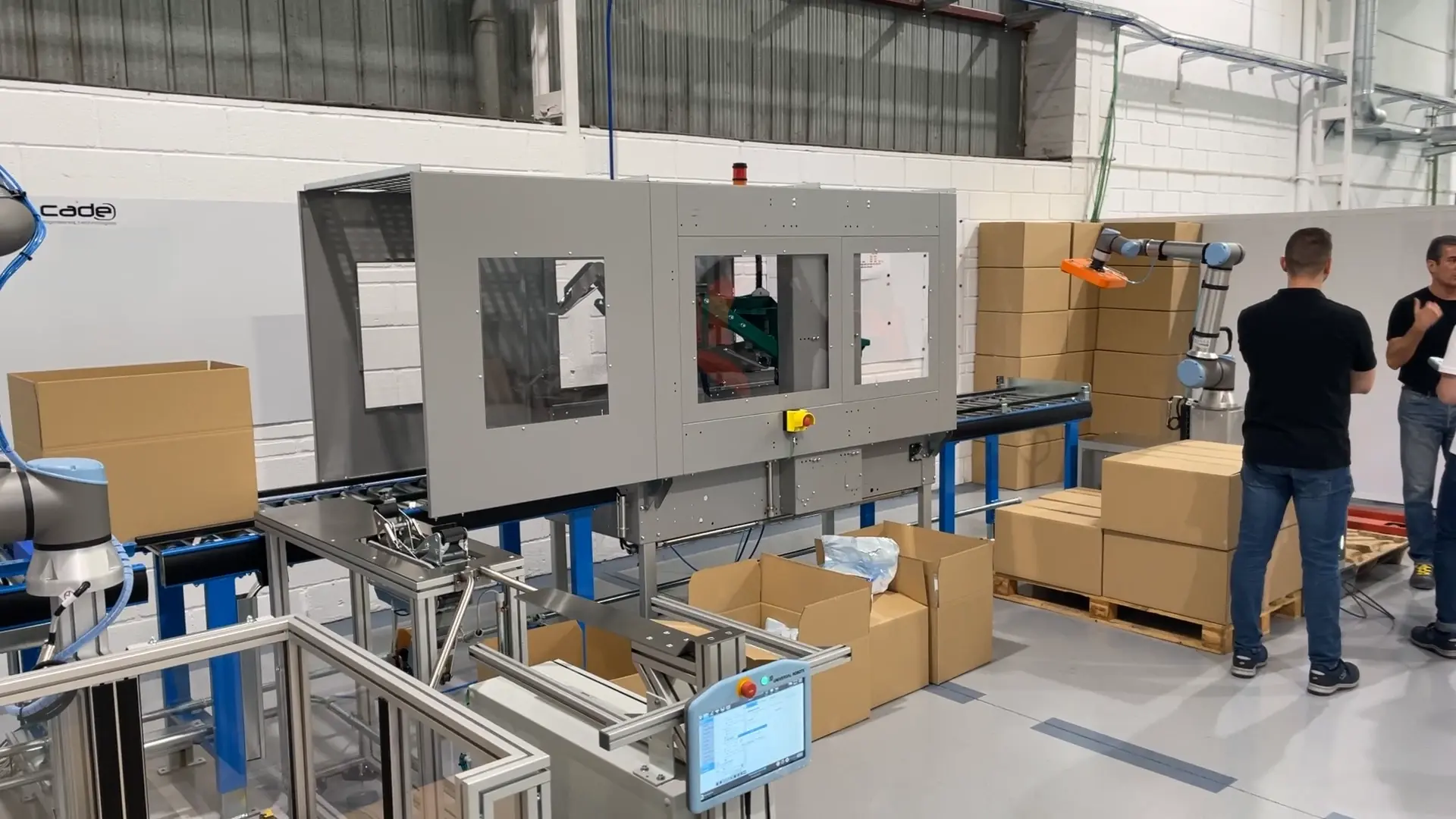
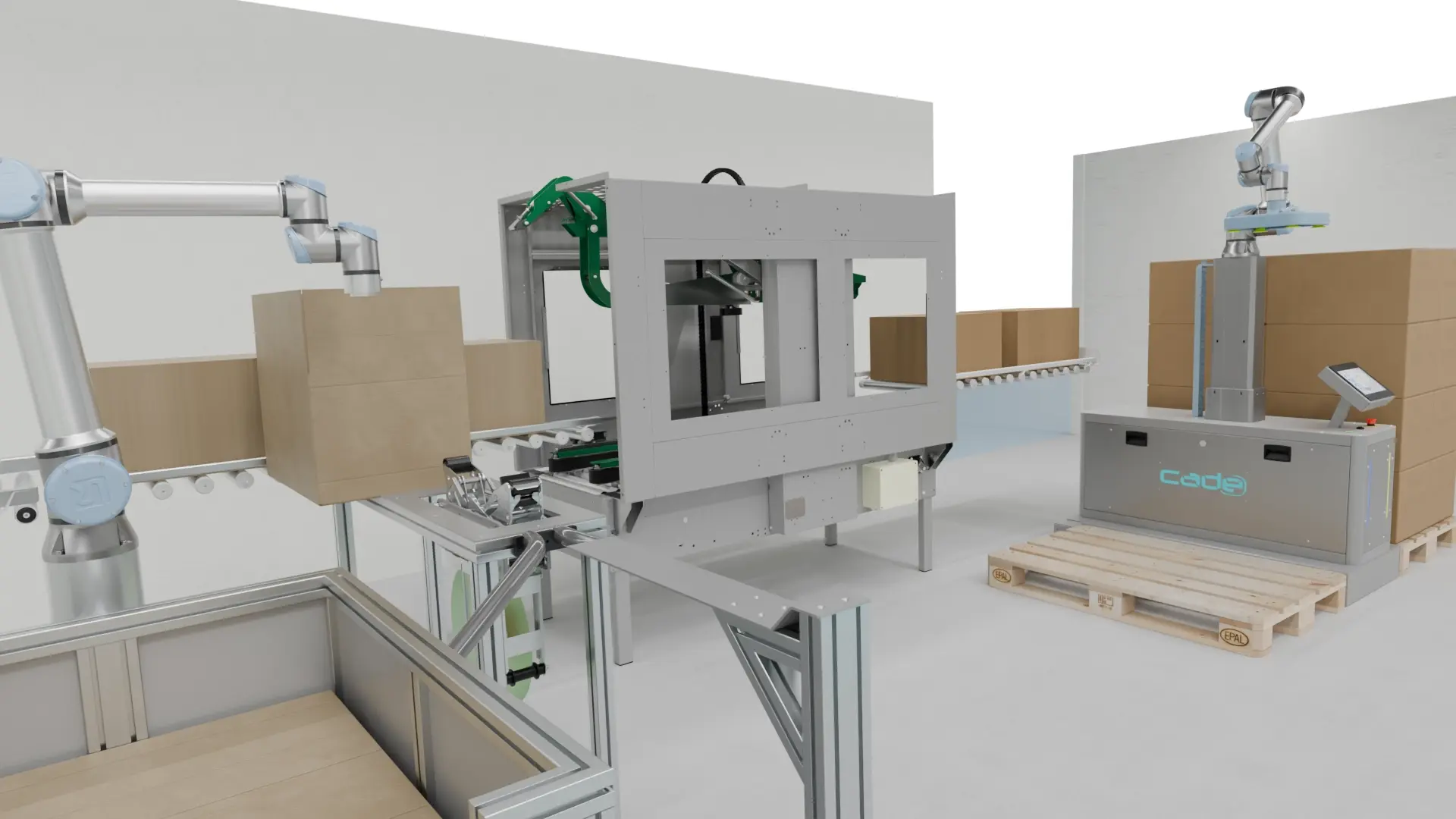