We Define and Ensure an
Integrated Welding Process Design
Identifying welding issues in industrial engineering projects to improve durability and reliability.
Welding Consulting
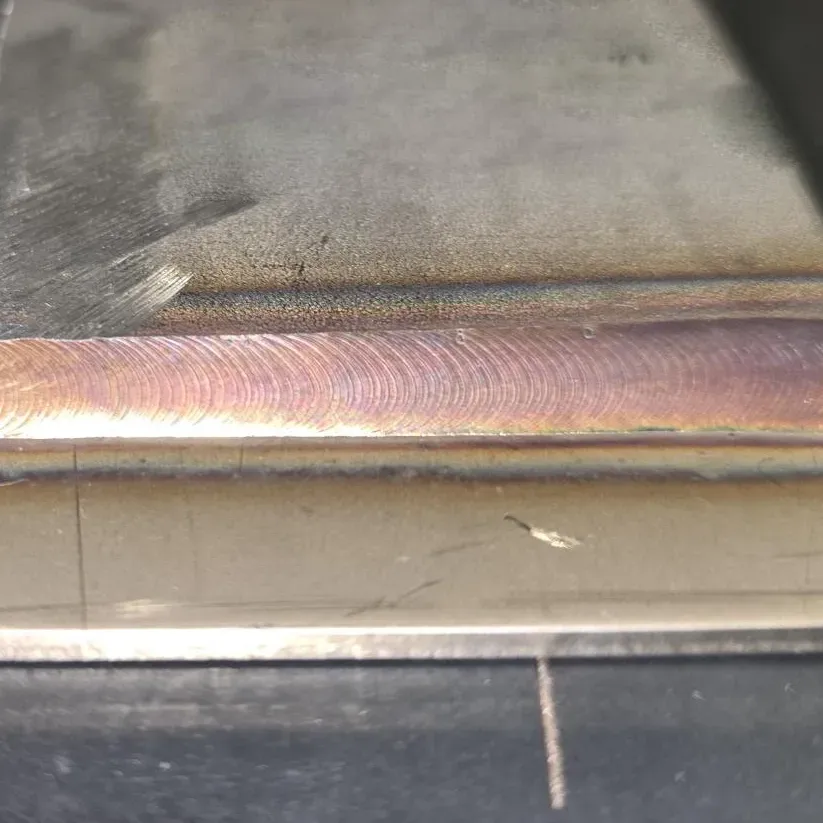
We define and ensure the quality, safety, and efficiency of welding processes in industrial and advanced engineering projects.
Our comprehensive approach covers everything from failure analysis to the full review of welding procedures and project documentation, ensuring compliance with the most demanding technical standards while optimizing resources and outcomes.
Whether tackling complex challenges in large-scale infrastructure projects or improving processes in manufacturing environments, we are committed to delivering solutions tailored to the real needs of each project.
Welding Failure Analysis
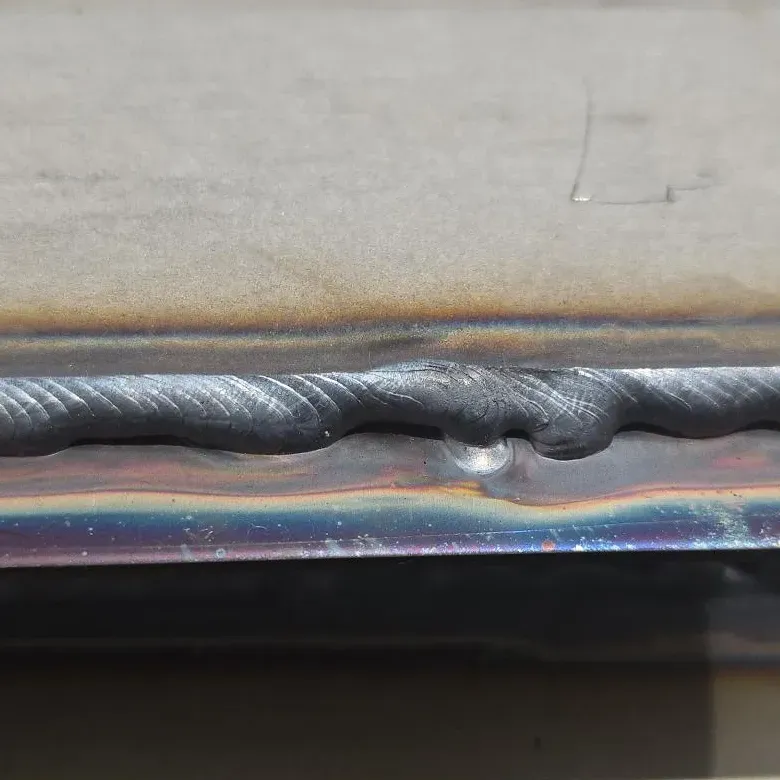
We have a team of welding engineers specialized in conducting thorough failure investigations to identify root causes of issues in welded joints. This service includes:
Detailed evaluation of welds and procedures
Analysis of operating conditions and materials used
Technical solutions to improve weld durability and reliability
Our failure analysis follows a systematic methodology using advanced diagnostic tools and techniques, providing critical insights into weld performance. We also offer actionable recommendations aligned with industry best practices and standards.
Benefits of Failure Analysis:
Accurate identification of underlying issues
Development of corrective and preventive actions to optimize structural integrity
Reduced repair and maintenance costs by improving operational efficiency
Prevention of recurrence by addressing systemic problems
Comprehensive Review of Welding Projects
Our consulting includes an exhaustive review of all welding process stages, focused on ensuring regulatory compliance and execution excellence.
Key Areas of Evaluation:
Procedure Qualification: We verify that welding procedures comply with project specs and applicable standards such as ASME BPVC, EN ISO 15614-1, and PED (2014/68/EU)
Welder and Operator Qualification: We assess technical competencies to ensure weld quality and compliance
Filler Materials: We review compatibility and properties of welding consumables
Preheat and Postheat Practices: We supervise techniques to reduce residual stresses and avoid defects
Post-Weld Heat Treatment (PWHT): We validate procedures to ensure structural integrity and long-term performance
We emphasize client collaboration to ensure all welding processes are optimized and aligned with project goals.
Benefits of Comprehensive Review:
Full compliance with international standards and quality regulations
Improved weld reliability and longevity
Risk mitigation during execution and optimized operational results
Detailed documentation to support audits and project certification
Review of
Methods, Capabilities, and Testing Results
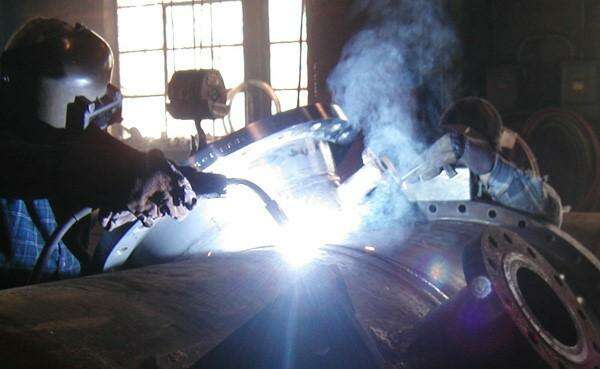
We perform a thorough evaluation of both destructive and non-destructive testing (NDT) methods, assessing procedures and results to ensure compliance with project requirements.
Types of Tests Reviewed:
Non-Destructive Testing (NDT): includes visual inspection, ultrasonic testing, radiography, and magnetic particle testing to ensure joint integrity without damaging the welds
Destructive Testing: includes tensile, hardness, and impact testing to provide essential data on weld mechanical properties
Our evaluations rely on advanced testing technologies and recognized international standards, ensuring result reliability.
Benefits of Test Review:
Guaranteed quality and reliability through verified testing methods
Early detection of potential defects or inconsistencies
Increased project confidence, supported by detailed test reports