Problem Definition
Vibration problems in process units are a common concern in industrial building structures that house dynamic equipment such as pumps, compressors, agitated reactors/tanks, centrifugal separators, thin-film evaporators, and coke drums. These vibrations can reach significant amplitudes, sometimes even visible to the naked eye, potentially causing structural damage and affecting operational efficiency. To correct or prevent these issues during the design phase, CADE deploys advanced dynamic analysis capabilities through finite element calculations.
Below is the dynamic analysis methodology using finite element analysis applied to a case study developed by CADE. The objective was to anticipate and limit potential vibration and resonance issues when installing new dynamic equipment in an existing process unit.
Main Objectives of the Vibration Analysis
Assess the influence of reinforcement structures for equipment support on existing structures through dynamic analyses.
Evaluate and analyze structural dynamics in the design of support structures for vibrating equipment.
Methodology
Modal Analysis: Frequencies and Resonance
Modal analysis is performed to obtain the natural frequency ranges of the structure, which are then compared with the excitation frequencies of each piece of equipment installed in the process building.
Objectives:
Prevent the natural frequencies of the structure from coinciding with the operating frequencies of the equipment, thereby avoiding resonance phenomena and vibration issues.
Results:
Identification of coincidences between natural frequencies and excitation frequencies.
Conclusion:
If resonance is detected, a Harmonic Analysis is conducted.
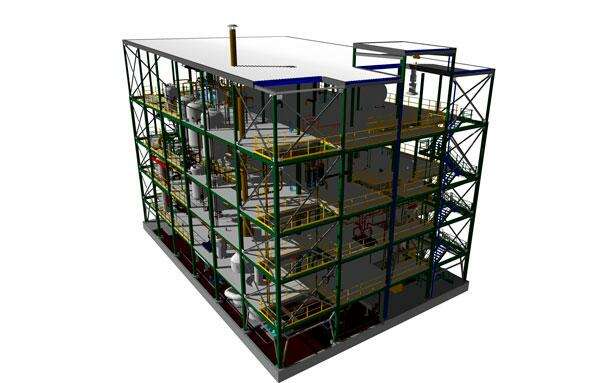
Harmonic Analyses
Several harmonic analyses of the structure are performed under two operating conditions:
Equipment fully loaded.
Equipment completely empty.
Harmonic loads are considered individually.
The objective is to determine the stress and deformation states of the structure within the operating frequency range of the equipment.
Displacement amplitude limitations are applied according to the code (CTE DB SE-A Steel).
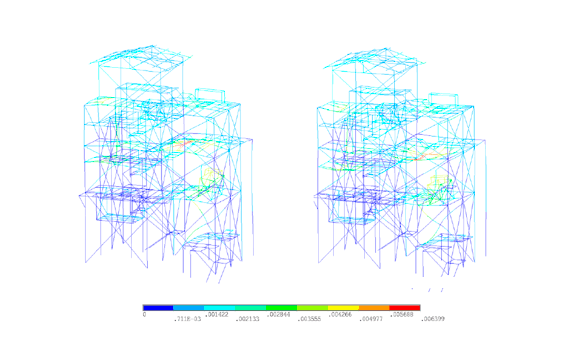
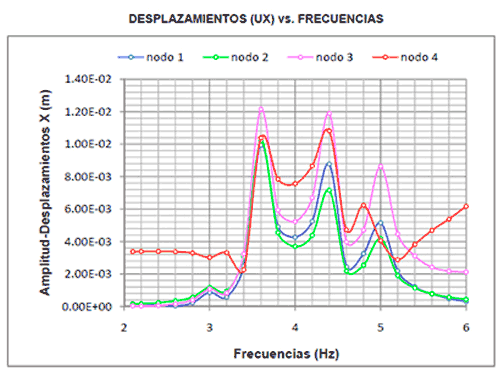
Conclusions
In response to the vibration issues of the installation, the causes and magnitude of the phenomenon are identified and quantified. Structural reinforcement solutions are proposed to mitigate the amplitude and severity of the problem.
Limitation of stress states and maximum displacements according to the code (CTE DB SE-A Steel).
About CADE Engineering Solutions:
CADE provides engineering, simulation, and consulting services focused on evaluating critical plant equipment and structures (including vibration issues) when performance is below expectations, failures occur, or when an assessment of mechanical integrity and remaining service life is required.