In our post “Additive Manufacturing (AM) integrated into collaborative robotics solutions” we discuss general concepts of 3D printing and the use of this technology by its Industry 4.0 department in its CADE LAB.
Next, we are going to present a practical case of an application of 3D printing in the machine designing, performed in the execution of a real project.
Content
Introduction
During the development of the design phase of one of the functional parts of a machine, the need arises to design baskets or containers to transport extruded rubber parts.
The premises are the following:
- The weight must be as light as possible to reduce motorization and, therefore, the installed power and consumption of the machine.
- The design must be functionally validated with the execution of several prototypes that also test the resistance of the assembly, so a highly flexible and fast route is required to incorporate changes.
- The development and manufacturing time is essential so the total time of development must be kept to a minimum.
- Commercial materials and components should be incorporated with minimal processing to facilitate maintenance.
- Finally, as in any project, costs must be kept to a minimum as long as the above requirements are met.
Development
The technical team quickly presents the convenience of leveraging in-house additive manufacturing capabilities to prototype quickly and at a low cost. Besides that, it allows undertaking quick changes in the pieces introducing the improvements identified in the prototyping.
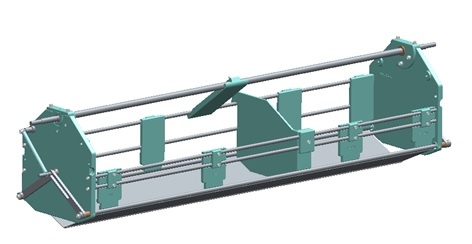
A cage-shaped structure is designed in a way that lightens the weight, but maintains the necessary rigidity and functionalities, with a combination of materials as follows:
- Onyx printing for the parts with the highest mechanical stress, that is, the stress concentrators around the transmission shafts.
- PLA printing for the rest of the plastic parts.
- AISI 304 stainless sheets of steel on shafts, tie rods, and bottom plates.
- Rest of commercial parts: screws, bronze bushings, and springs.
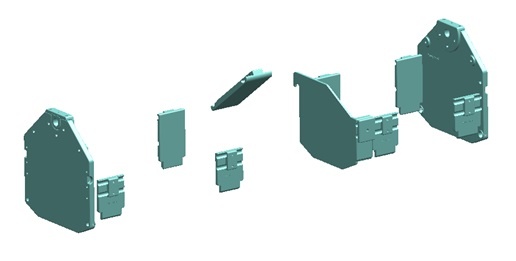
As we have previously mentioned, the time factor is critical and the chosen route provides very fast returns so that in a month the finished solution was available:
- Functional tests of the first prototype in 2 weeks.
- Functional tests of the second prototype 1 week later.
- Delivery of a final set assembled in 2 weeks.
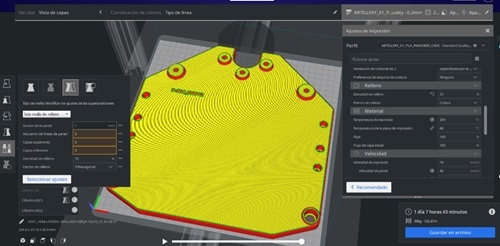
Conclusions
With the methodology described above, the incorporation of 3D printing into the design for this specific case has led to the following improvements:
- Reduction of the iterative prototyping time from 5 weeks, in the best case with a classical mechanical solution, to just 3 weeks. This represents a 40% reduction in the time required in this phase.
- Reduction of container delivery time from 4 to 2 weeks. 50% cut in manufacturing time.
- 30% reduction in weight from 19.2 to 13.4 kg.
- Manufacturing cost reduction by 35%.
Therefore, we can conclude that the integration of Additive Manufacturing technology in CADE’s Industry 4.0 developments is very positive thanks to the aforementioned improvements (delivery date, weight and cost), to which we must add others such as flexibility and independence. against third parties, positioning CADE in a more competitive position and generating value for the customer.
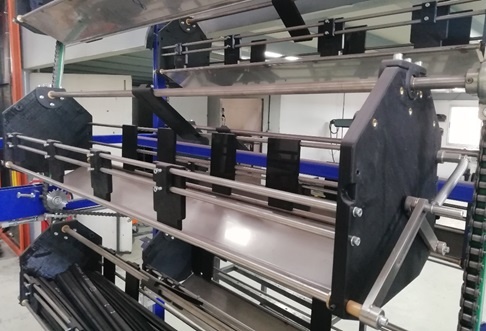
Further information:
For any question or further information request about our services and technologies, please complete the following form: