When deformations appear in existing storage tanks, both atmospheric and low pressure, which exceed the maximum defined in the API 653 standard, the immediate step is to analyze the serviceability of the equipment (1) to guarantee an acceptable level of safety and accurately determine its remaining life (2) as well.
(1) FFS – Fitness For Service Assessment
(2) RLA – Remaining life Assessment
Using the laser scanning tool
In order to model in detail the deformations that a storage tank presents, one of the most powerful tools is the use of laser scanning.
CADE has extensive experience both in the use of 3D laser scanner technology, obtaining precise and reliable measurements, and also in the processing of the point clouds obtained in the scan. Through this point cloud, it is possible to generate a model of the equipment that includes the real deformations with total accuracy.
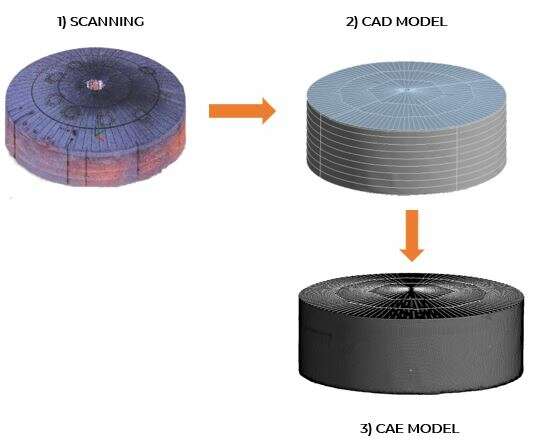
Fitness for service
The analysis of the suitability of a piece of equipment to continue in service carried out through fitness for service (FFS) assessment, by means of which the mechanical integrity of the tank that has suffered certain damages or presents structural failures that cast doubt on its ability to operate is evaluated. This FFS analysis applies not only to tanks designed according to API regulations but also to pressure equipment and piping designed according to ASME regulations.
It is essential to know the mechanisms of damage and the possible interaction between them, to carry out an adequate assessment of suitability for service. Other damage mechanisms apart from large distortions that call into question the work of the equipment in service are localized and generalized loss of material, corrosion, the appearance of cracks, laminations, misalignment in welding, among others
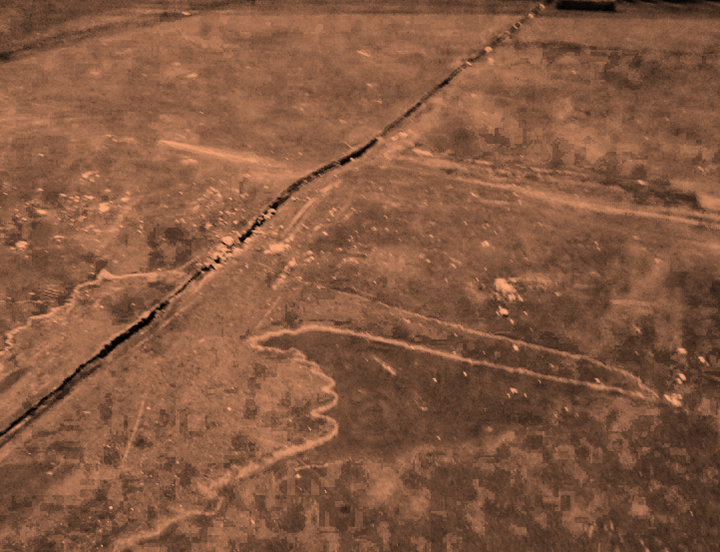
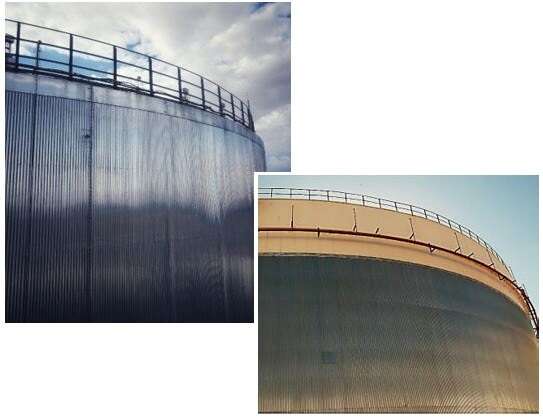
The API 579-1-ASME FFS-1 standard establishes three levels of Fitness for Service analysis. These three levels are progressive and the choice of one or the other will depend on the level of detail required. The acceptance criteria of levels 1 and 2 are much more conservative than those corresponding to level 3 because this level 3 is based on numerical methods such as finite elements that involve much more complex analysis.
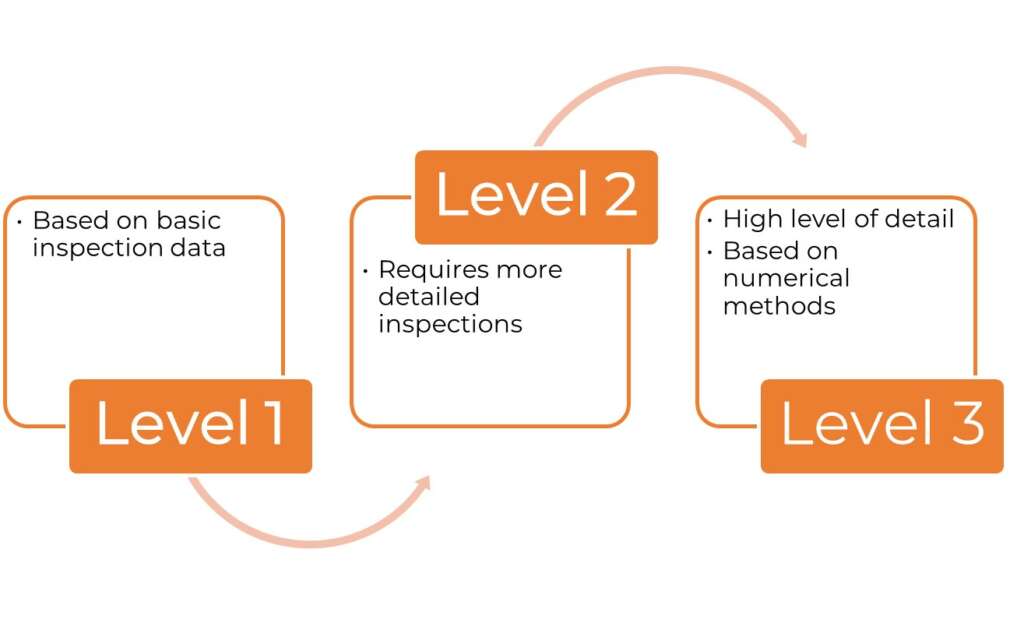
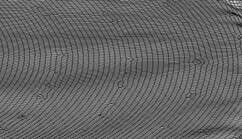
The advantages of performing structural analysis using finite elements are widely known, since it allows the determination of the stress states of damaged equipment with great precision. Being able to carry out these more complex calculations means that the acceptance criteria established by the API 579-1-ASME FFS-1 standard for a level 3 are more precise, which offers advantages not only from a reliability point of view and safety but also from an economic point of view:
- The precision of the results offered by a level 3 analysis can imply considerable cost savings, since it may be the case that equipment that has not passed the screening through level 1 and 2 analysis, if they are suitable to continue in service through the application of a level 3.
- This precision of results offered by a level 3 analysis allows for a detailed study of those critical areas that present geometric singularities or localized defects, which is always advantageous from a reliability and safety point of view.
In a level 3 FFS analysis, the failure modes considered are the following:
- Protection against plastic collapse
- Local fault protection
- Buckling collapse protection
- Fatigue protection
- Ratcheting protection
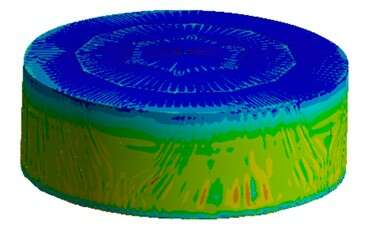
CADE has extensive experience not only in evaluating the integrity of equipment but also in performing 3D scans with its high-precision equipment and in processing the obtained point clouds.
Thanks to this extensive experience, the goal of FFS analysis at CADE is not limited to determining whether or not a piece of equipment is suitable for continued service life according to the minimum requirements established by the API 579-1/ ASME FFS-1 standard, but Preventive and predictive maintenance strategies are defined to avoid the repetition of these phenomena in the future. If a piece of equipment is not suitable for working in service, a study of suitability for service is carried out, analyzing possible corrective measures that make the equipment return to operation. These corrective measures can focus on partial repair or modification of operating conditions to mitigate the effect of the distortions found.
However, after the detection of certain defects that cast doubt on the capacity of the tank to continue providing service, another question that arises is what has been the origin of these deformations: We are able to answer this question through an RCA analysis ( Root Cause Analysis ).
Employing Root Cause Analysis (RCA), the identification of the causes that have originated the defects found and that have led to the equipment shutdown is sought (external actions, design / operating conditions that cause overpressures or thermal shocks, abnormal operating situations, faults in the control systems, etc.) as well as the understanding of the problems inherent to these possible causes, preventing them from being repeated in the future. The possible causes of the problem are not seen, so a more exhaustive analysis must be carried out to be able to identify them, using our multidisciplinary team specialized not only in advanced simulation but also with extensive knowledge in the operation and functioning of equipment. and plants, inspection of equipment, study of materials, corrosion mechanisms, etc.
All conclusions and root causes must be substantiated by documented evidence. In the RCA study, it is essential to clearly define a timeline in which the sequence of appearance of events is identified and in this way possible relationships between root causes are not overlooked.
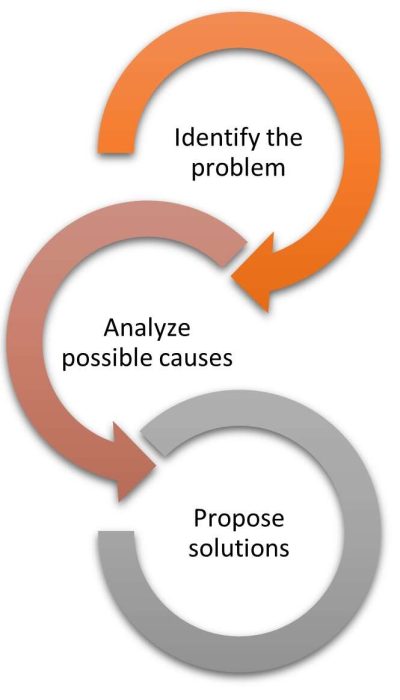
The main steps in the RCA analysis carried out by CADE are:
- Study of the problem
- Analysis of available documentation, history, and verified facts.
- Identification of possible failure hypotheses.
- Physical characterization of the problem
- Physical description of the problem.
- Simulation using FEA analysis.
- Evaluation of results obtained
- Hypothesis validation.
- Identification of possible solutions and corrective measures.
- Preparation of a final dossier.
CADE has extensive experience in carrying out structural analysis to evaluate the stresses and the stress state that may have caused the appearance of phenomena that have led to the instability and failure of equipment, with knowledge of metallurgy and corrosion mechanisms, mechanics of the fracture to evaluate the evolution of the cracks, knowledge of plant operations and processes. A good understanding of RCA analyses means that they can also be used, as lessons learned, as a preventive methodology to forecast possible failures before they occur.
Further information
For any query or request for additional information about our services and technologies, please complete the following form: