En nuestro post “Fabricación aditiva (FA) integrada en soluciones de robótica colaborativa” tratamos conceptos generales de la impresión 3D y el uso que de esta tecnología hace el Área de Industria 4.0 con su CADE LAB.
A continuación, vamos a presentar un caso práctico de aplicación de la impresión 3d en el diseño de máquinas llevado a cabo en la ejecución de un proyecto real.
Indice de contenidos
Introducción
Durante el desarrollo de la fase de diseño de una de las partes funcionales de una máquina, se plantea la necesidad de diseñar unas cestas o contenedores para transportar piezas extruidas en caucho.
Las premisas son las siguientes:
- El peso debe ser lo más liviano posible para reducir la motorización y, por lo tanto, la potencia instalada y consumo de la máquina.
- El diseño debe validarse funcionalmente con la ejecución de varios prototipos que prueben también la resistencia del conjunto, por lo que se requiere de una ruta de alta flexibilidad y rapidez para incorporar cambios.
- El plazo de desarrollo y fabricación es fundamental por lo que debe reducirse al mínimo el tiempo total.
- Deben incorporarse materiales y componentes comerciales con el mínimo de procesado para facilitar el mantenimiento.
- Por último, como en cualquier proyecto, los costes deben mantenerse en los mínimos siempre que se cumplan los requerimientos anteriores.
Desarrollo
El equipo técnico pone rápidamente sobre la mesa la conveniencia de aprovechar las capacidades internas de fabricación aditiva a la hora de realizar prototipos de manera rápida y con un bajo coste. Además de que permite llevar a cabo cambios rápidos en las piezas introduciendo las mejoras identificadas en el prototipado.
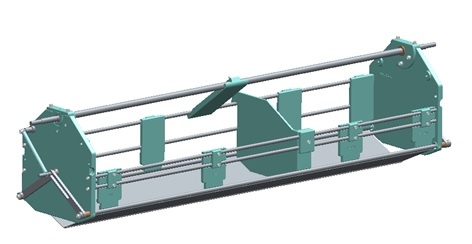
Se diseña una estructura en forma de jaula que aligera el peso, pero mantiene la rigidez y funcionalidades necesarias, con una combinación de materiales de la siguiente manera:
- Impresión en Onyx para las piezas de mayor solicitación mecánica, es decir, los concentradores de tensión alrededor de los ejes de transmisión.
- Impresión en PLA para el resto de piezas plásticas.
- Aceros inoxidables AISI 304 en ejes, varillas de atado y chapas inferiores.
- Resto de piezas comerciales: tornillería, casquillos de bronce y muelles.
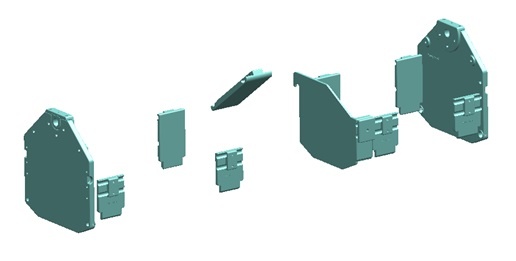
Como habíamos dicho, el factor tiempo es crítico y la ruta elegida proporciona unos retornos muy rápidos, de manera que en un mes se pudo disponer de la solución terminada:
- Pruebas funcionales del primer prototipo en 2 semanas.
- Pruebas funcionales del segundo prototipo 1 semana después.
- Entrega de un conjunto definitivo montado en 2 semanas.
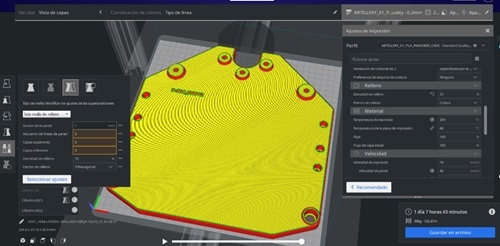
Conclusiones
Siguiendo la metodología descrita anteriormente, la incorporación de la impresión 3D al diseño para este caso concreto ha supuesto las siguientes mejoras:
- Reducción del tiempo iterativo de prototipado de 5 semanas, en el mejor de los casos con una solución mecánica clásica, a tan solo 3 semanas. Esto supone una reducción del 40% del tiempo necesario en esta fase.
- Reducción del tiempo de entrega de los contenedores de 4 a 2 semanas. Recorte del 50% del tiempo de fabricación.
- Reducción de un 30% en peso al pasar de 19,2 a 13,4 kg.
- Reducción del coste de fabricación en un 35%.
Por lo tanto, podemos concluir que la integración de la tecnología de Fabricación Aditiva en los desarrollos Industria 4.0 de CADE es muy positiva gracias a las mejoras anteriormente mencionadas (plazo, peso y coste), a las que debemos añadir otras como la flexibilidad e independencia frente a terceros, permitiéndonos una posición más competitiva y generadora de valor para el cliente.
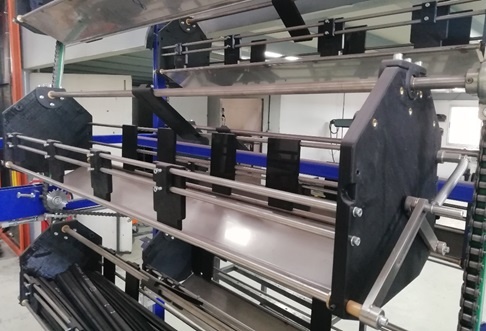