We Maximize the Reliability of Your Assets through
Asset Integrity and Performance Consulting
Multidisciplinary
Services and Capabilities
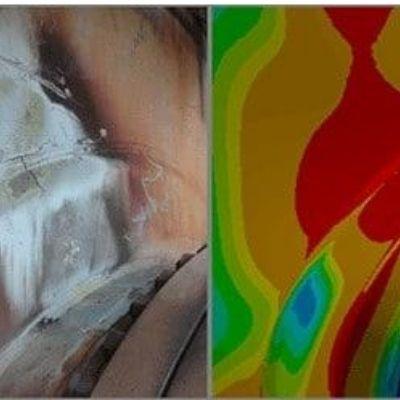
CADE’s Asset Integrity and Performance Consulting services bring together multidisciplinary expertise in engineering, simulation, and forensic analysis, aimed at assessing critical equipment and systems in scenarios where:
Performance is below expectations
A significant failure has occurred
It is necessary to determine mechanical integrity and remaining useful life
Assets commonly analyzed include pressure vessels, high-criticality piping, special structures, and large-diameter ducts, among others.
CADE is a benchmark in the development of Root Cause Analysis (RCA), thanks to its specialization in forensic engineering methodologies. These include process analysis, data handling, inspection, defect evaluation, and advanced computer simulation. Our approach covers every stage of a complete RCA:
On-site inspections and defect analysis
Historical data review and Distributed Control System (DCS) signal analysis
Material evaluation and lab testing
Failure hypothesis development and validation through FEA, CFD, and CHT simulations
Definition and verification of corrective actions
Fitness For Service (FFS) Evaluation
Fitness For Service (FFS) is an advanced, quantitative engineering assessment used to determine whether an operating asset is safe and reliable under predefined conditions for a specific period of time. FFS evaluations are considered a critical part of any mechanical integrity program.
An FFS assessment is necessary in the following scenarios:
When the original design documentation is unavailable or the asset has exceeded its expected life
For equipment operating at high temperatures and/or under cyclic conditions
For retired assets being considered for repurposed service
For assets affected by incidents such as thermal shocks, mechanical overloads, feedstock changes, or fire damage
When inspections reveal conditions that may impact the future behavior of the asset, such as:
Metal loss (due to corrosion or erosion)
Deformations (misalignment, dents)
Laminations or cracks
An FFS evaluation provides a solid basis for decision-making: whether to repair, replace, retire, or re-rate an asset.
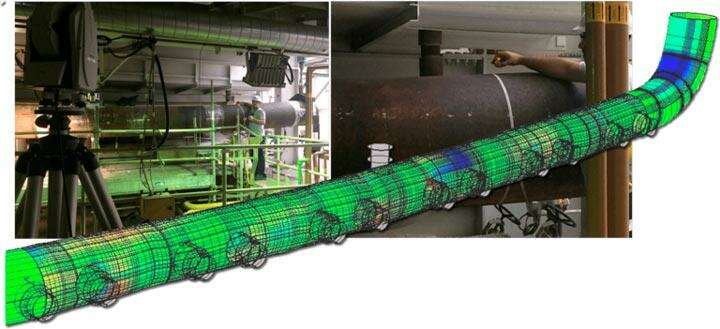
The primary benefit of FFS is to ensure safe and reliable operation. Additionally, FFS allows for the elimination of unnecessary repairs, helping to reduce downtime and maintenance costs.
Over the years, CADE has built deep expertise in FFS methodologies, successfully extending their use not only to operating equipment and systems but also to:
Manufacturing validation
On-site commissioning
Failure investigation in cases of mechanical or integrity issues
This methodology is commonly applied to thermal and process equipment, including heat exchangers, reactors, columns, and tanks.