We are currently immersed in one of the greatest challenges, and at the same time longing, of the industrial sector: having the largest and best amount of information possible in relation to its assets, processes and products.
Taking the foregoing as a premise, it is therefore essential to obtain, control and analyze fast and reliable data, as well as the automation of processes and systems to facilitate in some cases, and allow in others, rapid and correct decision-making by the of the owner, in relation to the operation and maintenance of its industrial plant.
Greater safety for people and processes, greater environmental and economic efficiency, and greater flexibility and adaptability to the needs and requirements of the market, are neither more nor less, the solutions that the concept of digitization has as its main objective.
For CADE, it is the so-called digital twin, together with advanced simulation, the tool/solution that, in its opinion, gives greater power to the concept of digitization and is the main lever for improving productivity and efficiency.
The increase of the analysis capacity through the digital twin allows, not only a greater knowledge of the processes and their improvement potential, but also the creation of new business opportunities.
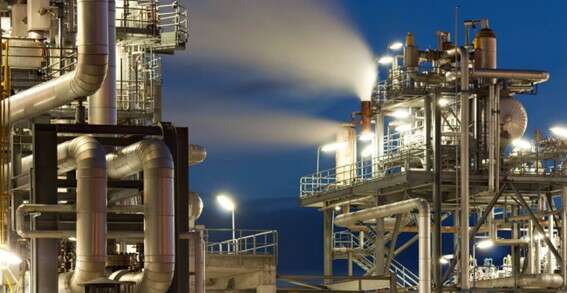
Content
What is a digital twin?
A digital twin is a connected virtual replica of a physical entity in service (a piece of equipment, a process or an entire plant). Sensors and devices embedded in the entity collect and transmit data in real time to a simulated model (digital twin); in this way, the captured data represents high-level information that integrates the behavior pattern of the digitized goods with the digital twin, allowing past behavior to be monitored, complete information about the present and, most importantly, helping to predict the future behavior, anticipating and acting on possible problems.
Real-time digital representation, provided by a digital twin, has great potential in which advanced simulation plays a key role. Thanks to tools based on the finite element method (FEM) and computational fluid mechanics (CFD), it is possible to simulate different processes in equipment and components of industrial plants, allowing both the evaluation of the process itself, and the evaluation of the thermal-structural behavior of said equipment.
These methodologies are used, therefore, as an analysis and optimization tool, improving the accuracy of behavior predictions and allowing the real implementation of predictive and prescriptive maintenance. As the digital twin is an exact replica of a product or process, with the same functionalities, it is possible to carry out various tests, as well as the validation of results in the digital twin.
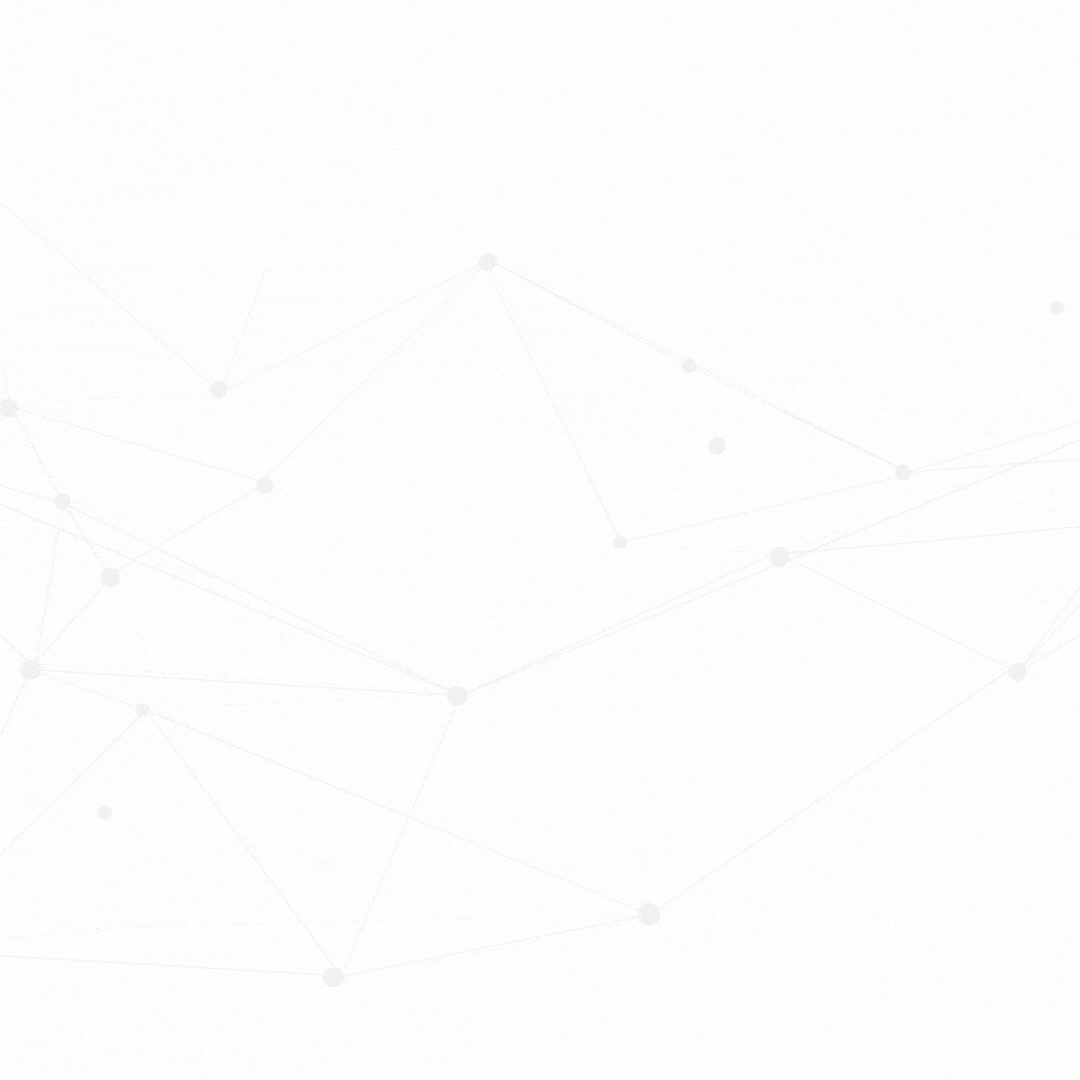
Industrial plants must be prepared to favor the operation of digital twins, that is, they must allow interaction with plant information in real time, so that the digital twin can realistically reproduce the behavior of the equipment or simulated process.
To ensure that the virtual twin offers a reliable virtual representation and, therefore, that the predictions about the real model are sufficiently precise, it is necessary to collect large volumes of information. In this process, it is essential to have tools such as the use of Artificial Intelligence (AI), Big Data and the Internet of Things (IoT) to provide power, storage capacity and data analysis.
Thanks to the integration of digital technologies, the models can be connected to the real world to work with updated information in real time.
Benefits of a digital twin
The implementation of a digital twin represents, among all, the following benefits:
- Improves the understanding of industrial processes.
- Allows both the identification of critical areas in the equipment, anticipating a possible failure of the same, as an accurate evaluation of the actual operating conditions of the equipment / process. Therefore, it is possible to predict possible incidents with both time and economic savings. Since it allows a problem to be identified before giving rise to a failure and, therefore, it allows a solution to be implemented very quickly and effectively.
- Improves the planning of associated maintenance plans, by having real-time information on the behavior of the simulated system or process.
- Facilitates the automation of traditionally manual tasks.
- Favors testing to improve the performance and productivity of the equipment / process.
- It allows virtual visits to be carried out, as well as the provision of training related to the operation of the equipment or process, thus avoiding the risks associated with the real environment.
CADE's experience and know-how
At CADE we are aware of the importance of advanced and quality engineering to enable the deployment of the industry 4.0 concept, as well as the role that digital twins play in this process of digital transformation. We have extensive experience in the use of tools that facilitate the digital twin implantation process:
- 3D laser technology to obtain precise and reliable measurements of the equipment to be represented and for the subsequent processing of the point clouds obtained in the scan. Through this point cloud it is possible to generate a model of the equipment with total accuracy.
- Simulation by finite elements (FEA) and computational fluid mechanics (CFD) through the use of advanced software.
- Collaborative robotics tools.
- Integration of digital technologies.
- Experience in the use of AI tools for the collection of information and processing of a large volume of data.
Further information
For any query or request for additional information about our services and technologies, please complete the following form: