Safety in hydrogen installations is a critical aspect in the modern energy industry. Throughout history, numerous incidents have demonstrated the serious consequences that can result from leaks in high-pressure systems, especially when dealing with flammable gases such as hydrogen, which have been recorded (h2tools.org) and analysed in detail forming a database of causes and lessons learned to be considered for the safe design and maintenance of hydrogen facilities.
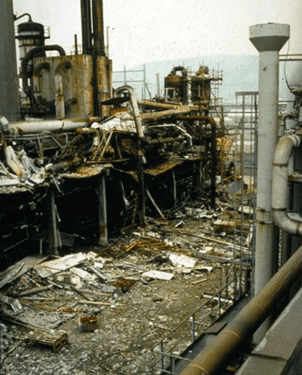
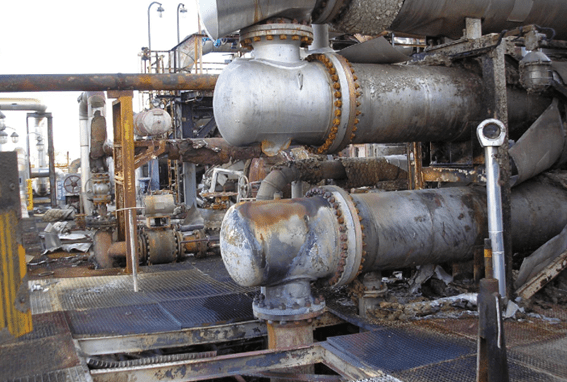
Estos eventos subrayan la importancia crucial de prever y prevenir fugas en tuberías y equipos a presión en el ámbito de la seguridad (Safety) de hidrógeno. En este artículo se aborda la clasificación de tipos de fugas, sus posibles consecuencias y cómo la mecánica de fluidos computacional puede contribuir a mejorar la seguridad en estas instalaciones.
Clasificación y consecuencias de las fugas
These events underline the crucial importance of anticipating and preventing leaks in pipelines and pressure equipment in the field of hydrogen safety. This article discusses the classification of leak types, their possible consequences and how computational fluid mechanics can contribute to improve safety in these installations.
- Primary Leaks (or micro-leaks): Leaks of small size and of a continuous nature over time, often difficult to detect without specialized equipment or laboratory tests. These leaks develop at a molecular level, due to diffusion and permeation effects, or due to microscopic leaks.
- Minor or Secondary Leaks: Leaks that are more significant than primary leaks, but do not imply a total failure of the piping or equipment where they occur. They can be caused by: :
- Cracks or fissures, which in turn can be caused by hydrogen embrittlement.
- Connection leaks
- Corrosion leaks
- Wear and tear leaks
- Major or Catastrophic Leaks: Being the largest leaks, they involve a sudden and massive release of gas.
- Complete pipe/hose rupture
- Pressure vessel failure
- Explosions
The consequences of hydrogen leaks can vary significantly depending on the type and magnitude of the leak:
- Efficiency loss: Even small leaks can result in decreased system efficiency and economic losses.
- Structural damage: High pressure leaks can cause mechanical damage to nearby equipment and facilities.
- Material embrittlement: Prolonged exposure to hydrogen can cause embrittlement of certain metals, compromising structural integrity.
- Asphyxiation: In confined spaces, the presence of leaks can displace oxygen, creating an asphyxiation risk for personnel.
- Fire hazard: Hydrogen is highly flammable (with a Lower Explosive Limit of 4% hydrogen in air) and with minimal energy required for ignition.
- Explosion hazard: In confined spaces, hydrogen can accumulate and form explosive mixtures with air.
Computational fluid mechanics in leak prevention and analysis
Although safety and zoning analyses are usually based on specialized standards (e.g. UNE-EN IEC 60079-10-1: 2022 for the classification of ATEX sites), there are a large number of studies (design, verification and validation, risk mitigation or forensic engineering) that require a detailed analysis of the leak to determine its characteristics, its dispersion over space and time, and the presence of contaminating clouds or the possibility of generating fire and/or explosion events that could endanger the integrity of the facilities and even the lives of people.
It is in these studies that computational fluid mechanics (CFD) has become an invaluable tool for predicting and analysing the consequences of leakage events in hydrogen systems and ATEX / ATOX facilities or facilities with polluting products. CFD calculation allows, among others:
- Leak characterization: Determine the composition and characteristics of the leak, analysing complex phenomena, such as the appearance of shock waves in supersonic regimes.
- Dispersion modelling: Simulate the dispersion of hydrogen or leak components, helping to identify risk areas and design appropriate venting systems.
- Fire/explosion risk analysis: Analyse the composition of the plume generated by the leak to compare it with the ternary fire/explosion diagram according to the dispersion of the leak components.
- Pressure and flow analysis: Study the behaviour of the fluid inside the piping and equipment, identifying stress points that could be prone to leakage.
- Design optimization: Evaluate different system configurations to minimize the risk of leakage and optimize safety.
- Simulation of leak scenarios: Model various leak scenarios to develop and test emergency response protocols.
- Detection system evaluation: Optimize the location and sensitivity of hydrogen detection systems.
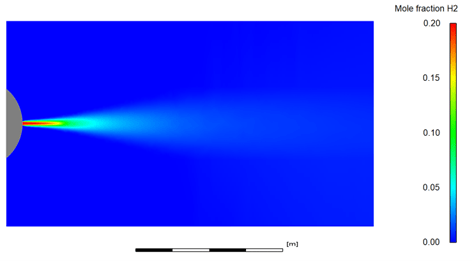
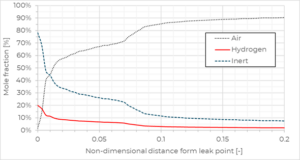
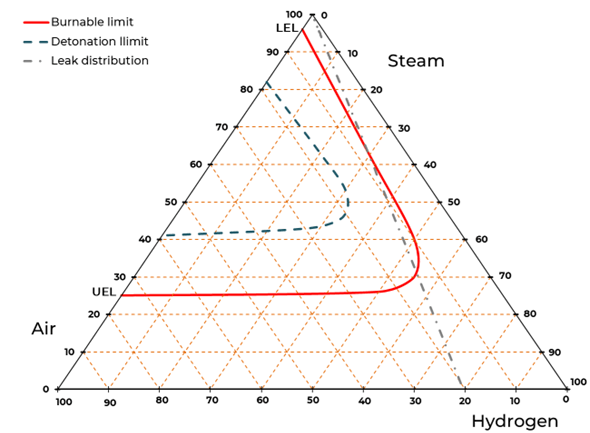
Conclusión
The prevention and management of leaks in hydrogen facilities is a fundamental aspect of industrial safety in the energy sector. The combination of meticulous design, proper material selection, rigorous maintenance protocols and the advanced use of tools such as computational fluid mechanics are essential to minimize the risks associated with handling high-pressure hydrogen.
As the hydrogen industry continues to expand as part of the transition to cleaner energy, the importance of these safety approaches cannot be underestimated. Investment in research, development of new leak detection and prevention technologies, and ongoing training of personnel are crucial to ensure a safe and sustainable future for the hydrogen industry.
CADE, with more than 20 years of experience in computational calculation, has a specialized team that can assist you in the design, verification and validation of your facilities and response protocols, providing expertise in:
- Classification and zoning of sites with hazardous concentrations (toxicity, flammability, explosiveness).
- Analysis of secondary and catastrophic leaks and evaporation from puddles.
- Evaluation of dispersion and dilution of leaks and concentration clouds in free atmospheres and confined spaces.
- Identification and structural analysis of areas affected by cryogenic temperatures and fire/explosion events.
- Evaluation of leak scenarios with fire/explosion risk or risks to equipment, structures and people.
- Design, verification and optimization of mitigation measures and ventilation and detection systems.
- Root cause analysis (RCA), within the area of forensic engineering, for the determination of failure causes.