Content
FFS BRUSHSTROKES
Definition of Fitness-For-Service (FFS) Assessment API 579-1/ASME FFS-1
Quantitative engineering evaluation to determine if an in-service equipment is safe and Reliable to operate at specific conditions during a Determined Time.
Normally FFS Assessment is applicable for Oil&Gas, Refinery and petrochemical, or Power assets like pressure vessels, pipes, tanks, among others. It is a valuable engineering tool when an asset lacks its original design information or it may have exceeded its useful life, for decommissioned asset that may be used in a different service, for equipment operating in either high temperature and/or cyclic service, or assets that have undergone any event that might have affected its serviceability like temperature excursions, overloads, different feed/external environment or a fire. Most of times it is applied when inspection findings revealed a condition that may impact the future operation of the asset, such as metal loss (e. corrosion/erosion), distortion (misalignment, out of roundness, bulges or dents), laminations, cracking or blisters, etc. and a fundamental decision is required (to repair, to replace, to retire, to rerate or to re-operate).
Obviously, main benefits of FFS are granting safe and reliable operation, but also allowing reductions in downtime by eliminating unnecessary repairs, giving extra time to plan shutdown and furthermore reduces eventual costs.
During last years CADE has applied successfully, and deepen his knowledge, in FFS methodology extending his application not only to in-service equipment, but also to post-fabrication acceptability, pre-commissioning validation or failure investigation support. We offer a multidisciplinary approach, mechanical and process oriented, and we have established partnering or ad-hoc collaborations with reputed inspection, verification, testing and certification firms to provide full integrity evaluation including non-destructive testing (NDT), materials testing, field services, visual inspection or notified body reports/services.
SCC Crack evaluation in heat exchanger bended tube
Fitness-For-Service (FFS) Background
Fitness for Service is a relatively new procedure, before 2000 there were no standards or Recommended Practices on Fitness-For-Service Assessment. The Materials Properties Council initiated activities in 1991 as a Group Sponsored Project. Original Scope was evaluation of pressurized equipment in the refinery and petrochemical industry, but then was extended to other industries. First edition was published in 2000 as API Recommended Practice API RP 579. ASME/API Joint Committee start activities in 2003, afterwards Second Edition of document ASME/API Standard was published in 2007 (API 579-1/ASME FFS-1). Example problems were published in 2009 (API 579-2/ASME FFS-2) (…)
Scope of FFS Assessment per API/ASME Standard API 579-1/ASME FFS-1
Assessment or re-rating of components designed and constructed to:
- ASME B&PV Codes Section VIII Division 1 & 2, Section I
- ASME B31.3/B31.1 Piping Codes
- API Standards: API 650/620
- Other recognized codes and standards, including International Standards (review attributes/compare to API & ASME codes)
- Methods and procedures intended to supplement API 510, API 570, and API 653
What happens to in-service equipment?
- Time dependent degradation
- Upset operating condition (Pressure, Temperature)
- Fluid – Material Interaction
What need to be done?
- Inspection (original fabrication and in-service flaws)
- Maintenance (including repairs and replacement)
Guidelines to make run-repair-replace decisions of in-service equipment are required.
Failure conditions and types of flaws
- Brittle fracture
- Fire damage
- Metal loss due to corrosion/erosion (general, local, and pitting)
- HIC damage (blisters, HIC, SOHIC)
- Geometrical irregularities (weld misalignment and distortion)
- Crack-like flaws (Amine cracking, Ammonia cracking, Carbonate cracking, Hydrogen damage (H2S, HF), Hydrogen attack, Caustic cracking in SS, Chloride cracking in SS, Polythionic cracking in SS)
- Creep
- Dent and gouges
- Laminations
API 579-1 / ASME FFS 1 content (2nd Edition)
- Part 1: Introduction
- Part 2: Fitness-For Service Engineering Assessment Procedure
- Part 3: Assessment of Existing Equipment for Brittle Fracture
- Part 4: Assessment of General Metal Loss
- Part 5: Assessment of Local Metal loss
- Part 6: Assessment of Pitting Corrosion
- Part 7: Assessment of Hydrogen Blisters and Hydrogen Damage HIC & SOHIC
- Part 8: Assessment of Weld Misalignment and Shell Distortions
- Part 9: Assessment of Crack-Like Flaws
- Part 10: Assessment of Components Operating in Creep Regime
- Part 11: Assessment of Fire Damage
- Part 12: Assessment of Dent, Gouges, and Dent-Gouge Combinations
- Part 13: Assessment of Laminations
- Annexes
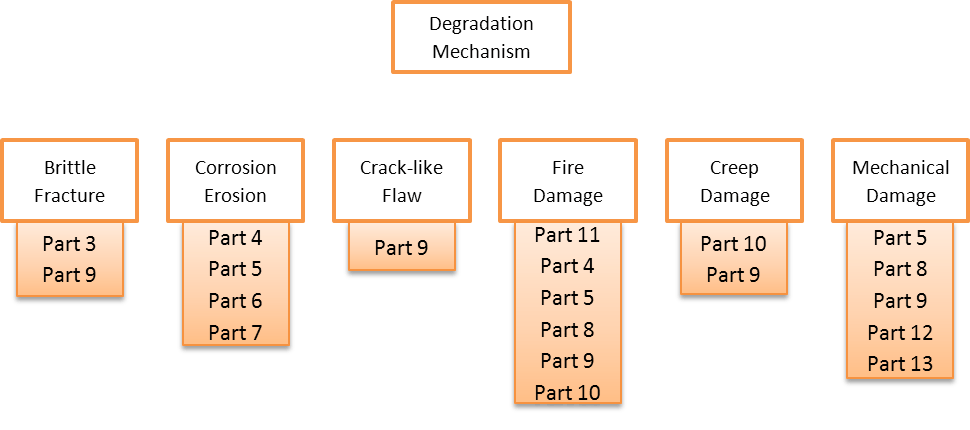
Evaluation Techniques
Assessment Levels
LEVEL 1:
- Conservative screening
- Minimum amount of inspection or component information
- Plant inspection or engineering personnel
LEVEL 2:
- More detailed: less conservative with more accurate results
- Inspection information
- Qualified engineering personnel
LEVEL 3:
- The most detailed evaluation
- The most detailed inspection and component information
- Recommended analysis procedures based on material testing and/or numerical analysis techniques such as the Finite Element Method
- Personnel with expertise in Complex FFS Assessments
General Assessment Procedure / Steps
- Step 1 – Flaw/Condition Identification (Mode of Failure)
- Step 2 – Applicability and Limitations
- Step 3 – Data Requirements
- Step 4 – Assessment Techniques and Acceptance Criteria
- Step 5 – Remaining Life Evaluation
- Step 6 – Remediation
- Step 7 – In-Service Monitoring
- Step 8 – Documentation
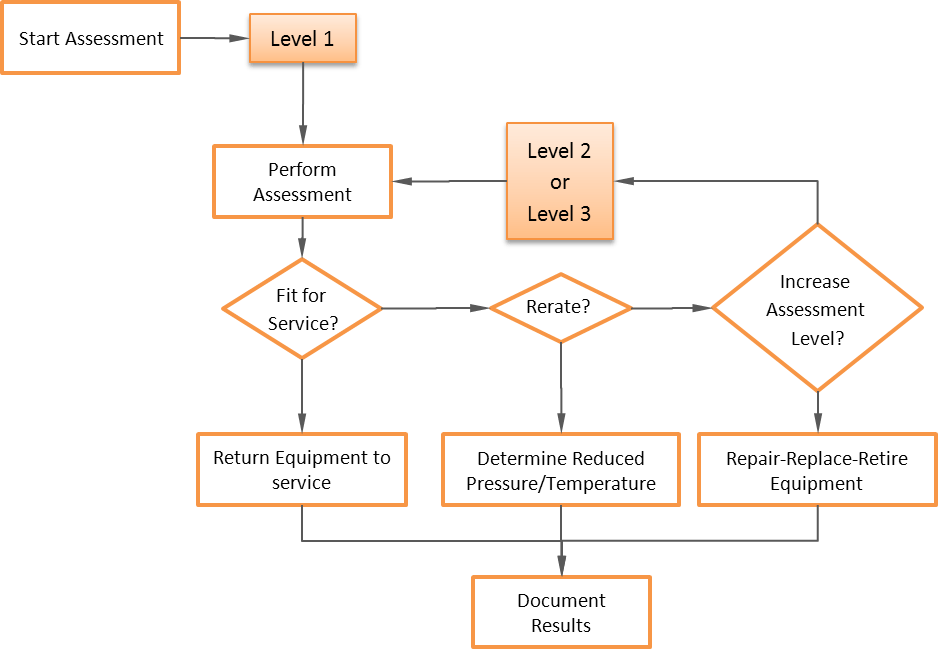
Further information about Fitness For Service Assessment:
For any question or further information request about FFS assessment, please complete the following form: