In the developmet of the current legislation on major accidents, there have been several European Directives that have been defining the current legal framework, creating the SEVESO legislation (SEVESO I, SEVESO II y SEVESO III). This legal framework has been updated periodically, taking into account the main lessons learned from industrial accidents occurred in the past.
The analysis of incidents showed:
- The majority of incidents could have been anticipated if a systematic risk-based approach had been used throughout the life of the system.
- Safety principles are independent of the technology.
- Situations often missed through lack of systematic approach.
Within this legal framework, industries are obliged to draw up a Safety Report with the following objectives to demonstrate:
- That a major prevention policy and a safety management system have been established.
- That major accident hazards have been identified and that the necessary measures have been taken into account to prevent them and limit their consequences.
- That the design, construction, operation and maintenance of any facility, storage area, equipment and infrastructure associated with its operation and related major-accident hazards are sufficiently safe and reliable.
- That internal emergency plans have been developed, and the elements enabling the development of the external emergency plan have been provided.
- And to ensure that sufficient information is provided to the competent authorities.
This report should be reviewed at least every 5 years, or at any time at the initiative of the industry itself, at the request of the competent authority, in case of changes in process, etc…
Content
Methods of risk identification and analysis
Ir order to comply with point 2, it is necessary to develop a Process Hazards Analysis (PHA), with the aim of identifying the hazards and qualitatively, semi-quantitatively or quantitatively assessing the risks in any process, in order to minimise the most of them, or at least, to control them.
There is a common saying in the control systems world ‘If you want to control something, first make sure you can measure it.’ We need to control the risks of harm or losses in the workplace due to hazards of all forms. So what we need to measure is RISK.
Here we need to be clear on the terms ‘Hazard’ and ‘Risk’.
A hazard is ‘an inherent physical or chemical characteristic that has the potential for causing harm to people, property, or the environment. In chemical processes, ‘It is the combination of hazardous material, an operating environment, and certain unplanned events that could result in an accident.
‘Risk is usually defined as the combination of the severity and probability of an event. In other words, how often can it happen and how bad is it when it does happen? Risk can be evaluated qualitatively or quantitatively.’
Roughly,
Risk = Frequency × Consequence of Hazard
Table 1 shows the classification of existing methods for risk identification:
Qualitative methods |
Semi-quantitative methods |
Quantitative methods |
---|---|---|
HazOp studies
|
SIL/LOPA studies
|
RCA (Quantitative Risk Analysis)
|
HAZID studies
|
FMECA (Failure Mode, Effects and Criticality Analysis)
|
ETA (Event Tree Analysis).
|
Check list
|
|
FTA (Fault Tree Analysis
|
What-if Analysis
|
||
FMEA (Failure Mode and Effects Analysis)
|
Table 1
It is necessary to use each one according to the installation and the stage of the life cycle it is in. As a selection criterion, Table 2 can be used as a reference:
Preliminary risk analysis (PRA) |
Check list |
What-if Analysis |
HazOp |
Fault trees |
Event trees |
|
---|---|---|---|---|---|---|
R&D Processes
|
|
|
|
|
|
|
Pilot Plants
|
|
|
|
|
|
|
Basic Project
|
|
|
|
|
|
|
Detailed Engineering
|
|
|
|
|
|
|
Work execution and commissioning
|
|
|
|
|
|
|
Normal Operation
|
|
|
|
|
|
|
Modifications
|
|
|
|
|
|
|
Incident and Accident studies
|
|
|
|
|
|
|
Process abandonment
|
|
|
|
|
|
|
Table 2
The Hazard and Operability Study (HAZOP)
This method is based on the rigorous, systematic, guided and critical checking of the processes and design bases of process plants, estimating the Hazard potential that could be generated by handling error sor malfunctions, and assessing the consequences for the installation itself, for people and for the environment.
It can be applied to all types of process facilities (such as refineries, pharmaceuticals, etc.), including power generation facilities (combined cycles, solar termal power plants, etc.), fuel storage and distribution facilities, etc.
Its objectives include:
- To review the design of the process to ensure the safe operation of the plant.
- Verify the existence of deviations resulting from control or operational failures that may involve harm to people, facilities or the environment.
- Ensure that sufficient safeguards (layers of protection) have been included in the design, to reduce the risk to a tolerable level (ALARP).
A HAZOP study requires a multi-disciplinary team, including personnel from different departments, such as Safety, Process, Engineering, Operations, etc., with sufficient knowledge and experience of the process, decisión making and commitment.
What information is needed to carry out a HAZOP?
- P&IDs, PFDs.
- Process description, material and energy balances.
- Operation and Maintenance manuals.
- Functional description of the control system
- List of main equipments and data sheets.
- List of hazardous substances and Safety Data Sheets.
- Interlock matrix.
- Installation Layout.
Development of a HAZOP study
As mentioned above, it is a systematic study, in which a complex process or even procedures are divided into nodes to facilitate the conduct of the study.
How are the nodes chosen? There is no specific way to do this, but we can give some guidelines for choosing them:
- They should have a similar function.
- It is better to study the main equipment separately (e.g. distillation columns, reactors…).
- In heat exchanger trains, it is better to carry out the study by circuits.
- Large nodes should be avoided.
- Nodes can even be process operational modes.
Once the nodes have been defined, the next step is to analyse the different process parameters: pressure, level, Flow, temperature, services (cooling water, electricity, instrument air, nitrogen for blanketing…), changes in streams composition… and to analyse, using the guide words, all possible scenarios, their causes, the consequences for each cause, and the safeguards that exist to reduce/mitigate the consequences to an aceptable level of risk. Where the leve lof risk is not acceptable, recommendations will be made to reach the acceptable leve lof risk.
The following figure shows the procedure to follow for the anaysis of a node
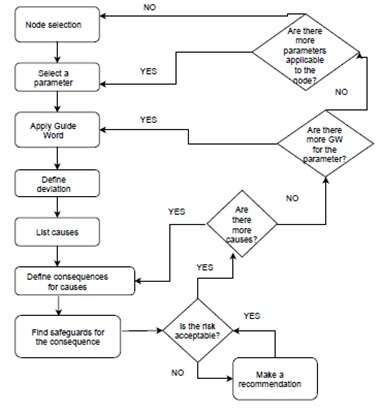
We also show an example of where the different parameters are usually analysed with the combinations of guide words:
Parameter |
Guide word |
Where it is often used |
---|---|---|
Pressure
|
More, less
|
In any type of equipment
|
Level
|
More, less
|
In vessels, columns, reactors, etc.
|
Flow
|
More, less, no, inverse
|
Usually covered by pressure, except in case of different feed and backflow inlets
|
Temperature
|
More, less
|
As long as there are heat tracing, heat exchangers or possibility of temperature change
|
Services
|
Loss
|
Instrument air, electrical power, cooling water
|
Contamination
|
Part
|
In case of tube ruptura of heat exchangers.
|
Composition
|
More, less
|
Its is often seen in equipment where very different streams are fed, in case of very acidic or basic streams can cause problems. Also in compressors, when heavy or light compounds can arrive to
|
pH
|
More, less
|
Sames as composition
|
Time
|
More, less
|
Batch operations
|
At CADE we carry out our projects by applying design codes and standards, prioritising good practices in the safe design of installations and analysing our clients’ processes always from the perspective of safety.
Further information
For any query or request for additional information about our services and technologies, please complete the following form: