Sewage depuration, seen from a simplistic, general point of view (omitting some treatment secondary processes) is no more than a series of processes aimed to eliminate suspended or dissolved solids in a pond of water which is required to be as purest as possible.
Every regular wastewater flow / sewages treatments are pretend to perform operations of filtering, coagulation, flocculation, sedimentation, flotation, precipitation or digestion, in order to try and obtain solids able to be separated from the main water flow.
However, these processes are not always as effective as desired, and the seeking of greater purity of the water obtained or greater dryness of the sludge withdrawn, which tend current depuration techniques, ends up generating a series of problematic flows whose treatment often has no place in conventional systems, and are eventually managed as waste, being diluted again with other effluents (arguably as good practice), and being intended to evaporation in ponds.
These sewages generated are, though, mostly water (up to 95%) and hence an important resource that must try to be fully exploited, avoiding them to become an additional cost for the company.
In this respect, since many years ago, systems have been in use for treatment of sewages, as Vacuum Evaporation. This technique, inherited from evaporated systems invented on the alimentary industry, is based on the decrease experimented by the boiling temperature of a water flow when under conditions of very low pressure (vacuum).
Nowadays, vacuum evaporation equipment allows extracting water from the fluid with a temperature about 35oC, thanks to depressions generated up to 33 mbar within the evaporation chamber. Nevertheless the problematic associated to these equipment is that the greater the concentration of solids in a liquid, because the evaporation of water, the greater the boiling temperature, until it reaches a “critical point” in which temperature makes the evaporation unfeasible (even though it is subjected to vacuum conditions).
Thus, although the result obtained by vacuum evaporation is more than satisfying, because what it gets is to reduce 90% to 95% the volume of the incoming waste stream, obtaining a concentrate that can be managed as a waste with a much lower cost than originally planned, at the end of the day you still have a highly concentrated liquid flow, problematic in terms of their management, and continue without reaching the long awaited “Zero Discharge”.
At this point is where CADE technology takes charge through INNOSPRAY®, a spray dryer system by atomization of great yield and low cost, that bases its performance on increasing the effective contact surface of the residual inlet flow mixing it with a hot air flow that eases a quick dry of the drop generated.
The spray drying technology is not a breakthrough in the markets. As well as vacuum evaporation, Spray Dryers have an extensive background in certain industrial environments such as alimentary or pharmaceuticals, where they have been used since the early of twentieth century as high-cost processes for totally drying liquid products and getting them as powder or even encapsulate them. Now, these systems are finding on the environmental sector a new field of application which requires adaptation to be economically viable and functional, something that has already reached INNOSPRAY®.
The core of these equipment is in their atomization system, which can be through rotating disks, nozzle under pressure (hydraulic or pneumatic) or even ultrasound, and the goal of them is to get the lowest drop size possible, and greater uniformity in the mist generated, being the size of the drop among 9 µm and 250 µm.
Their configuration will also vary according to the goals to be reached and the flows treated, and thus we can find in the market different possible alternatives about the mix with hot air, either in parallel, in countercurrent or through mixed flow.
The temperature and the way of generating the drying gas will also depend on the type of fluid to be treated and what you want to do with it. If the flow is not thermal-sensitive nor require of a subsequent recovery (as in many waste streams), there will not be a limit on the temperature of the inlet gas, and also it will be possible to introduce in the chamber the exhaust gases from the burner, something that would not be recommended otherwise.
In any case, at the end what is achieved is a completely dry particle (about 4% of humidity) of controlled granulometry that can be easily handled thanks to its small volume and solid state without generating the contamination risks of a liquid, and with a management cost much lower due to its smaller volume. All of this not to mention the possibilities open with the potential of compounds or water stream recovery, which can also be condensed to its exploitation.
Must be taken into account whenever evaporate sewage is, after all, to evaporate water, and thus means an energy cost for the company that does not escape the conception of CADE to provide its clients expert solutions to close the cycle and definitely resolve their problems.
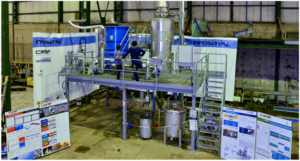
This way, INNOSPRAY® technology does not appear in CADE portfolio as an isolated solution but it is offered on an integrated way as part of the company’s technological solutions. Consequently, the equipment exploitation costs are reduced to minimum by seeking for the most appropriate solutions in every case, depending on the existence of residual heat flows, alternative process fuels, or even the possibility of applying new alternative technologies, as solar thermal power, or processCSP, to generate process heating and cooling.
Click here to read the full article (only is Spanish)