When dealing with the design of pressure equipment (heat exchangers, reactors, process columns, etc.), we can find certain design and operating conditions for which, in addition to having to guarantee an appropriate structural resistance, we must ensure adequate performance in the presence of corrosive environments or elements.
The alternative to the uneconomical solution of using resistant materials, but which would require much thicker sections to prevent future corrosion, is called cladding:
Cladding is a method by which we will obtain a suitable material at a reasonable cost, consisting of low-cost base material with excellent mechanical properties (such as carbon steel), and another material resistant to corrosion, abrasion or oxidation, that covers it, such as stainless steel, titanium, monel or duplex, among others.
Cladding techniques
The main cladding techniques are: Roll Cladding, Explosive Cladding, and Weld Overlaying:
- Roll Cladding: consists of laminating the base material (carbon or stainless steel) together with the coating resistant to corrosion, abrasión, or oxidation that were assembled and welded around its perimeter prior to the rolling process; thus achieving a resistant and homogeneous union between both materials. It is important to bear in mind that the coefficients of thermal expansion of the base material and that of its coating do not differ significantly, in order to avoid the appearance of areas where an adequate bond is not achieved. This method will not be suitable for large material thicknesses, since a great reduction in thickness will be needed to achieve a correct joint, making it extremely difficult to manufacture.
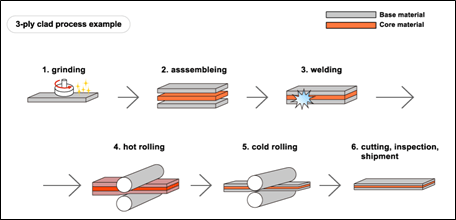
- Explosive Cladding: consists of joining the base material, carbon or alloy steel, to the coating resistant to corrosion, abrasión, or oxidation, detonating an explosive placed on both materials. This method allows the joining of materials with great thicknesses and joining carbon steel with titanium, which cannot be done with other techniques.
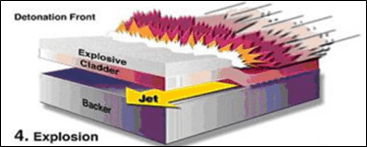
- Weld Overlaying: it is a welding process where a filling material resistant to corrosion, abrasion, or oxidation is deposited on a base material to give it those properties that are not typical of the base material. This technique is also used to return the original dimensions (for example thickness) to a certain component of the equipment
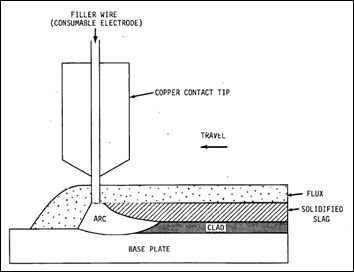
In conclusion, the design of each pressure equipment must be studied independently, considering the manufacturing costs related to a solid or clad construction (cladding), and the cost of the materials to be used in each case, taking as a reference the thicknesses obtained by prior mechanical calculation.
Further information
For any query or request for additional information about our services and technologies, please complete the following form: